What Are Aerospace Countersinks and Why Are They Essential?
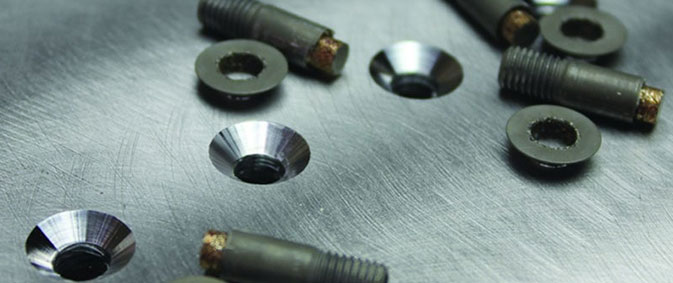
- February 28th, 2025
- Categories: Uncategorised
In aerospace, fasteners and tooling need to tolerate incredibly high temperatures and perform without fail. Countersink holes are used in metalworking, woodworking, and manufacturing industries and are critical to aircraft manufacturing and maintenance.
Without them, aircraft can fall apart. Aerospace countersinks ensure that aviation components are safe, reliable, and perform the way they should when in flight.
This blog will dive into the purpose, importance, types, methods, and benefits of aerospace countersinks, along with best practices for their use.
Aerospace Countersinks: An Overview
Aerospace countersinks are to allow fasteners (such as screws or rivets) to sit flush with or below the surface of a material. Let’s look at what countersinking holes are:
- The outer edge of a hole has been opened up to the conical entry, such as a 100-degree angle for BA threaded fasteners
- The countersink is sized according to the head dimensions of the fastener being fitted (such as flat-faced fastener)
- Plugs or caps can be fitted, rendering fasteners invisible
- Creating exterior ridges, a countersink hole helps to materials from hard materials
- Ideal for small designs with less installation space, the levelled surface provides more surface area, which is useful in tight, compact applications
What about countersink tooling? This is how to drill a countersink hole!
Firstly, countersinking is performed as a secondary job once holes have been formed or drilled. This countersink tool does not cut at the centre of rotation.
As specialist drill bits and cutters, they can have multiple cutting faces. Larger countersinks (For machine use) commonly have only one flute/cutter. This supports the centering on the hole and produces a more even and regular cut.
Countersinking can be performed manually or by machine and involves a specialist cutter. This creates a conical recess.
Types of Aerospace Consumables
Let’s look at the different types of aerospace countersinks and why they are essential to a safe flight.
Traditional Countersinks
Also called Single Flute Countersinks, these are the most common type of countersink used in the aerospace industry. These are basic, single-purpose tools or modifications designed to create conical recesses in a material.
With a single cutting edge, they are used in simpler applications (softer materials) or where a single fastener type is standardised.
Combined Countersinks
Also called Multi-Flute countersinks, these integrate drilling and countersinking into one operation.
With multiple cutting edges (ideal for harder materials), these reduce operational steps and improve alignment for a consistent finish.
Countersinks help fasten and join components, quickening the manufacturing processes for engineers!
Methods for Creating Aerospace Countersinks
What are some of the best countersinking methods for aerospace?
Tools Used for Countersinking
Creating a precise aerospace countersink requires specialised tools, including:
- Countersink Cutters These are conical tools used to create the recess.
- Microstop Countersink Tools Designed for precision depth control, these tools are essential in aerospace applications.
- CNC Machines For automated and highly accurate countersinking operations.
Techniques for Precision Countersinking
- Pilot Hole Drilling Ensures the countersink is perfectly centred and aligned.
- Depth Control Using tools with adjustable depth settings to avoid over- or under-countersinking.
- Material Compatibility Matching the countersink tool’s material and geometry with the aircraft component to prevent damage or imperfections.
Importance of Countersinks in Aircraft Components
All components must meet strict quality standards, and without proper countersinking, the exposed heads of fasteners can lead to:
- Increased drag during flight.
- Interference with movable parts (such as flaps or landing gear).
- Reduces weight reduction and makes sure fasteners don’t cause stress points. A lighter aircraft consumes less fuel and offers better payload capacity.
- Fasteners such as screws or rivets don’t protrude, which can weaken the materials
- Increased susceptibility to corrosion and wear. Exposed fastener heads can create snags, posing risks to both operational safety and maintenance efficiency.
- Removes burrs left behind from drilling or tapping operations to remove sharp edges
Aircraft manufacturers and maintenance teams rely on countersinks to meet aerospace engineering requirements.
Zephyr Tool Group: Engineered to Perform
Zephyr aerospace tools (from angle drills to attachments and accessories) meet the demands of commercial and military markets and are built to last. Every tool in the range has been created to increase productivity, improve strength and precision, and include an easy-to-use configuration capability. Let’s look at a few countersinking tools!
ZT334 Microstop Countersink Cage Shaft Thread (7/16”-20)
What are some of the features of the ZT334 Series?
- Can hold a Max Cutter Diameter of 1-½”
- They are precision machined and designed for continuous high-speed and heavy-duty operation without overheating
- Eight types of foot pieces for each model will fit all needs
- Simple, accurate, and dependable
ZT613 Angle Drills: 90 Degree Light Duty
This consists of a steel thrust block, generated bevel gear, ball bearing, steel housing, shielded ball bearing, ground steel spindle bearing, and the hardened ground drive shaft.
ZT33006 Microstop Countersink Cage
- Provides precise depth control by limiting the travel of the cutter being used and aiding in the perpendicular alignment of the cutter to the surface being matched.
- Used as a depth stop when countersinking or counterboring.
- Extremely accurate adjustment in increments of .001”.
- Accepts the industry standard ¼” x 28 TPI UNF threaded tooling up to ⅝” diameter.
ZT616 Angle Drills: 90 Light Duty
This is a small drill that does a big job in aerospace projects. It is designed for use in limited space and features a greatly reduced 90-degree end section, plus all the advantages of other Zephyr light-duty drills.
If you would like to learn more about aerospace tooling and what works best for your project, have a read of a beginner’s guide to understanding aerospace consumables.
FAQs for Aerospace Countersinking
1. What are the key dimensions to think about when designing countersink?
- You must understand the major diameter, which is large and at the top where the screw head will sit
- Minor diameter, which is smaller and at the bottom of the opening
- The angle of the rivet head or screw
2. What are the standard angles used for countersinking designs?
- 82 degrees for screws in U.S manufacturing
- 90 degrees for ISO 9001:2015 parts
- 100 degrees for fasteners in the aerospace industry
- 120 degrees for rivets
3. How can hardware selection impact countersink angles and measurements?
The hardware size, type, and materials determine the countersink measurements and angles. Selecting the correct hardware ensures it is compatible and prevents collisions between components.
4. What are the main approaches for applying countersinking to parts?
- Machined countersinks are made using tools such as drill presses or end mills. For low-volume orders and prototypes, the laser cuts the through-hole to the minor dimension, and this is followed by drilling a conical hole for the hardware.
- Formed countersinks are made with CNC punch presses. They form countersinks by punching a hole, then shaping the screw hole. Ideal for larger orders.
5. Are there any standards for aerospace countersinking?
Yes, aerospace countersinks often adhere to standards like AS9100 or company-specific engineering specifications to ensure safety and performance.
Do you need specialised tools for countersinking? Whether you need nylon foot pieces, aerospace countersinking kits and cages, Microstop Units, or countersink cutters, AFT supplies high speed steel, carbide, and diamond tooling.
Countersink Tooling: Contact Applied Fasteners and Tooling
If you are looking for custom product solutions, Applied Fasteners and Tooling is a reliable partner known for exceptional quality and delivery for all fasteners and tooling needs.
Registered and AS9120 quality certified in 2014, AFT was founded to supply the aerospace and defence industries with specialised fastening products and technical support. Emerging as a leader in the fastening system supply chain, we support you through the design, procurement, production, quality, maintenance and repair.
Contact us today by emailing support@aft.systems and shop our brands in stock! From Motorsport Fasteners to Hi Lok Tooling, Drilling Equipment, Cable Tie Mounts and Countersink Tooling, we are always happy to help and push the boundaries of what is possible.