Best Practices for Installing Marine Bonded Fasteners
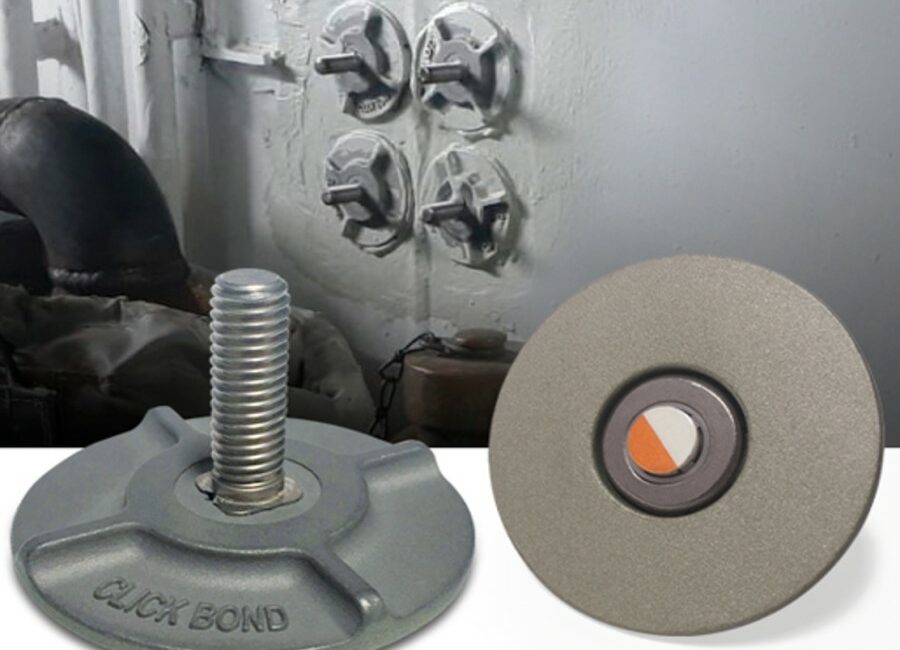
- March 25th, 2025
- Categories: Uncategorised
Bonded fasteners are incredibly important to the Marine sector. However, like any component, they need to be installed and fitted correctly. In order to deal with unique factors like salt water, wave height and fluctuating temperatures, it’s essential to use the correct fasteners, as well as the proper bonding and adhesion techniques.
Throughout this blog, we will explore marine bonded fasteners in detail, as well as the benefits, materials, and bonding recommendations for a successful installation.
Major Benefits of Marine Bonded Fasteners
Let’s take a look at some of the benefits of marine-bonded fasteners and how epoxy bonding strengthens them!
They are resistant to corrosion. Epoxy bonding eliminates the need for metal-on-metal contact in some cases, so it reduces the risk of galvanic corrosion when dissimilar metals are in contact with seawater.
They have a durable structure. Since it creates a bonded surface, epoxy fasteners distribute loads more evenly across the substrate, reducing stress concentrations and reducing the likelihood of it failing.
They offer a watertight sealing. Unlike mechanical fasteners (which can create openings for water intrusion), epoxy bonding creates a seamless seal to prevent leaks, rot, and corrosion.
They are lightweight. Epoxy bonding means you don’t need bulky hardware, which improves vessel performance, reduces weight, and improves aerodynamics.
Why aren’t standard fasteners suitable for marine applications? Conventional fasteners are not made to handle maritime settings as they don’t have the corrosion resistance to guarantee durability and security in saltwater environments.
Choosing the Right Type of Fastener for Marine Applications
How do you choose a bonded fastener for your project? It depends on load requirements, material capability, and environmental exposure.
- Threaded studs are great for mounting hardware securely as they provide a reliable attachment point for equipment that need to be reinstalled or removed altogether.
- Insert nuts offer a durable embedded threading option for easy disassembly and reassembly of components.
- Flat plates and bases give projects a stronger foundation for securing equipment, spreading loads across a larger area and cutting back stress concentrations.
- Bonded bushes and sleeves are used to reinforce holes and mounting points. They prevent wear and make your project last longer.
Do you work in other sectors of aerospace and defence? Read about Duocel metal ceramic foam and its commercial applications
Material Selections for Marine-Grade Fasteners
When planning a project with marine-graded fasteners, each material has a different use. Here are some grades to consider:
316 stainless steel, which has excellent corrosion resistance against saltwater and chlorides, and molybdenum for resistance. It is commonly used in deck hardware, rigging, and boat construction.
304 stainless steel, which is less corrosion resistant than 316 but is stronger than standard steel. 304 is suitable for freshwater and less aggressive marine environments.
Silicon bronze. It is more durable than brass, resists dezincification, and is used for below-water-line applications and through hull fittings
Monel, a nickel-copper alloy, has exceptional corrosion resistance in harsh saltwater environments. They are best for high-stress marine applications such as propeller shafts, submarine fasteners, and offshore platforms.
Titanium is high-performing for marine vessels and aerospace/military applications such as submarines, naval ships, weapons systems, ballistic armour, jet engine components, offshore oil and gas platforms, and propulsion systems.
Always think about the material’s exposure to saltwater, strength requirements, cost, performance, and material compatibility with surrounding metals.
Military Grade Fasteners by Click Bond
Click Bond fasteners exceed industry standards for marine applications. For example, the Insulation Blanket Mount Retainer is used to attach equipment, insulation blankets, panels, tubing and holes, cables, wiring, lighting and sensors.
Adhesive bonded Mounts by Click Bond offer enhanced design flexibility for routing of system and protective blankets in both new construction and retrofit applications.
Bonded attachment eliminates drilling and compromising structural integrity, cost, and restrictions from stress.
The Large Base Stud permits a clamped attachment of systems to structure or securing of enclosures or other modular equipment. They are supplied with disposable installation fixtures.
Importance of Surface Preparation Before Bonding
Before the bonding process begins, it is critical to prepare the surface you’re working on. So, what should you focus on?
Clean the surface and remove grease, dirt, and oxidation using acetone or isopropyl alcohol so epoxy bonds properly.
Sand or abraded to create a rough surface to increase the surface area for better epoxy adhesion. This ultimately improves the bond strength.
Make sure all surfaces are completely dry before applying epoxy to avoid moisture contamination, which weakens the bond.
Apply a primer, as some materials require a primer to enhance epoxy adhesion and improve bonding performance.
A Step By Step Guide to Epoxy Bonding for Marine Fasteners
Installing screws and other threaded fasteners dramatically improves load-carrying capacity by spreading the fastener’s load into a greater area of the substrate. There are many levels of hardware bonding depending on the hardware load.
Epoxy bonding secures fasteners in marine, aerospace, automotive, and construction applications. Here is a guide to proper preparation, mixing and application:
Surface Preparation
Clean the surface by removing dirt, grease, and contaminants using acetone, isopropyl alcohol, or a degreaser.
Sand the bonding area with grit sandpaper to improve the adhesion, then remove dust with a clean cloth and solvent, such as alcohol. Make sure the surfaces are dry and oil-free before applying epoxy.
Mix Epoxy Correctly
After choosing a marine-grade epoxy for fasteners, create a 2:1 or 1:1 resin-to-hardener ratio; use a clean mixing container to avoid contamination.
Mix the epoxy slowly for up to 3 minutes until it’s fully blended and get rid of any air bubbles.
Application Techniques
Apply epoxy to the fastener by coating the threads, shank, or base of the fasteners with a thin, even layer of epoxy. Use a brush or syringe for threaded fasteners.
If you’re embedding the fastener into a drilled hole, partially fill the hole with epoxy before inserting the fastener. Avoid overfilling!
Push or twist the fastener into place for full epoxy contact with the surface, and remove excess with a clean rag. You can use clamps, tape, or a fixture to hold the fastener securely while the epoxy cures.
Finally, follow the manufacturer’s instructions for curing time (typically 6 to 24 hours for full strength). Avoid applying any stress or load until the epoxy is completely cured.
If you are looking to make reliably watertight fastener penetrations through FRP laminate, there are things you can do that work well for through-bonding.
For bolts, you can drill out one size larger, then put a piece of tape over the downside, fill it with epoxy adhesive, and let it harden. When you hard drill it out to the correct size, insert the bolt.
For bonding fasteners, 30% to 40% larger diameter is the usual recommendation
Precautions When Working in Marine Environments
There are a few things to keep in mind when working with epoxy.
- Always work within the recommended temperature range for epoxy curing to avoid any weak bonds.
- Make sure there is proper airflow when handling epoxy resins, as fumes are harmful when inhaled.
- Wear goggles and gloves to prevent skin and eye irritation from epoxy chemicals
- When it comes to moisture control, avoid bonding in high-humidity conditions as this causes contamination and weaken the adhesion.
- You also want to weigh up the curing time. Be aware of environmental conditions that shorten or extend epoxy curing times. After all, you want a complete, secure bond before use.
What about maintaining marine-bonded fasteners? Some brief guidelines for care include:
- Frequently check fasteners for corrosion or loosenings.
- Clean fasteners and lubricate them with a corrosive-resistant substance. Replace fasteners that show noticeable wear or corrosion in protection against seawater exposure.
- Use sacrificial anodes to protect fasteners against galvanic corrosion.
Can galvanised fasteners be used in maritime applications? Although galvanised steel offers some corrosion resistance, prolonged exposure to seawater isn’t advised.
If you would like to learn more, have a read of marine bonded fasteners and their comprehensive applications!
Marine Bonded Fasteners: Call Applied Fasteners and Tooling
Registered and AS9120 quality-certified in 2014, Applied Fasteners and Tooling offer you the best of specialised fastening products and technical support.
We give aerospace and defence industries a personalised interaction and a value-added service throughout the product life cycle, procurement, production, quality, maintenance and repair. From aerospace consumables to GripLockTies, Click Bond fasteners, Hi Lok fasteners, motorsport fasteners and EMI/RFI shielding, we supply top-quality products.
Contact us today to get a quote and learn more about our quality assurance procurement requirements, markets, and services.