Why Are Honeycomb Inserts Important in Military Applications?
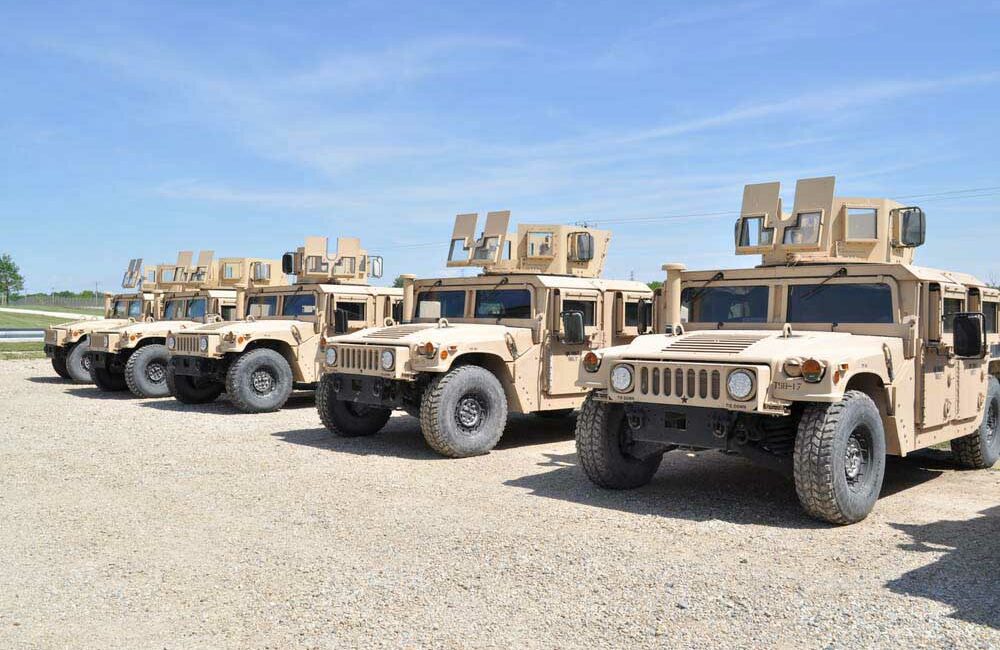
- April 01st, 2025
- Categories: Uncategorised
According to this article by Science Direct, the geometry of bee honeycombs has inspired technical designs in various fields, from architecture to transport and mechanical engineering, and a honeycomb sandwich structure has continued to be used in the defence sector.
In the military, materials need to be almost indestructible, and honeycomb inserts offer superior strength, lightweight properties, and excellent energy absorption for these critical applications.
From top-secret military missions to aircraft safety when surveilling suspicious sites, honeycomb inserts improve the performance of military vehicles, aircraft, and protective structures. Overall, they are non-negotiable components to keep military personnel and civilians safe.
This comprehensive guide explores the structural design, material modelling, manufacturing processes, quality assurance, and real-world applications of honeycomb inserts in the military sector.
Honeycomb Inserts: How Do They Help?
Honeycomb inserts are sandwich panels used to protect civil and military targets, and they help in a number of ways.
- Protect buildings and facilities from explosive attacks.
- Protect ships from mines or reduce the effects of shockwaves from underwater explosions.
- When applied to ballistics, honeycomb panels absorb shock waves and shrapnel, and retain fragments.
- In comparison to normal kinetic absorption strategies, composite materials offer modular solutions with low space consumption.
- By mixing materials with different properties, the composite material combination has superior mechanical characteristics of lightness and strength than individual materials.
- Honeycomb inserts are easily assembled and replaced.
- Honeycomb inserts are lightweight and easy to transport.
There is an application for every material requirement. For example:
- Polypropylene is a rigid material with good thermal insulation and resistance to water and moisture.
- Technical fabrics can increase the fabric’s properties; para-aramid fabrics stop perforations.
- The thick aluminium structure absorbs impacts since it has the ability to deform.
Structural Design of Honeycomb Inserts
Let’s take a closer look at honeycomb inserts and their technical specifications. What do they offer?
- High Strength-to-Weight Ratio: This ensures durability without adding a lot of weight.
- Energy Absorption Capability: Reduces the impact force transferred to the surrounding structure.
- Resilience Under Extreme Conditions: This maintains performance in high-temperature and high-stress environments.
When military design components need higher strength-to-weight ratios, the honeycomb sandwich structure provides the desired structural, thermal and acoustic insulation.
The sandwich is used as a sheeting or flat panel form applied to an open framework as a transverse web to carry sheer loading. In other applications, it acts as a support diaphragm, serving as both a primary and secondary load member.
It is capable of transmitting extremely high loads when properly attached to the framework. Other applications take advantage of its favourably low weight-to-area weight ratio, and fabrication techniques have resulted in bolder forms such as compound curves, skeletonised and many complex shapes once considered impossible.
Honeycomb Sandwich: The Structural Details
The principal form of the sandwich structure is the honeycomb configuration. This consists of the top and bottom face sheets attached to an inner core material made from hexagonal cells with walls perpendicular to the face sheet planes.
Many materials have been used successfully in a honeycomb sandwich, including steel, aluminium, high-temperature alloys, wood, paper, plastics, and fibreglass.
In some applications, honeycomb cells are filled with foam-in-place expanding plastic. Other forms of sandwich consists of face sheets bonded to homogenous cores such as foamed plastics or wood. The variety is limited only by the state-of-the-art and the imagination of the designer.
Joining Methods
Regardless of form, there are numerous methods for joining the two face skins and inner core into a rigid member. Let’s take a look at some of them!
- Brushing or spraying the adhesive film over one surface and subsequently mating with the second part precoated with an activator.
- Prefabricated sheet adhesive. The adhesive is rolled into a thin sheet partially cured to retain form and stored between temporary non-adhering film ready for use.
- Applying the adhesive with rollers to a scrim or grid cloth. This is then cut to size and applied between core face skins.
- An even coating of adhesive on the face skin is activated before setup.
In all of these methods, the development of optimum strength depends on the proper preparation of face skins and controlled application of adhesive to form optimum fillets between mated ends or faces of the core structure. Such bonding optimisation achieves even transmission of loads from face skins to core without rupturing the bond.
Other forms of sandwich structure (which offer high-temperature strength) performance are composed of all steel honeycomb and face skin. This offers the most resistance welded or brazed construction.
Composite Double-Layer Honeycomb Structures
With two layers of honeycomb cores, composite double-layer honeycomb structures are designed to boost mechanical performance. These layers may have different cell sizes or materials to enhance stiffness and energy absorption.
In military applications requiring high-impact resistance (armoured vehicles and aerospace components), double-layer honeycomb structures provide superior protection under high-speed impacts by dissipating energy and reducing the risk of catastrophic failure.
What about fracture energy calculations? These help engineers predict how honeycomb inserts will behave under different loading conditions. These calculations involve analysing the material’s stress-strain behaviour and failure mechanisms.
In composite double-layer honeycomb structures, understanding fracture energy ensures that the inserts can dissipate impact forces, preventing catastrophic failures in critical military applications.
What Are Some of the Manufacturing Processes for Honeycomb Inserts
Let’s take a look at the production of honeycomb inserts:
- Expansion Process: Produces traditional honeycomb core structures by stretching and bonding sheets of material.
- Corrugation Method: Involves shaping materials into a corrugated pattern before bonding them together.
- Moulding and Forming Techniques: Used to create complex geometries for specific applications.
The most popular honeycomb manufacturing methods of sandwich panel construction are the heated press, which is used for flat board or simple panels, or vacuum bag processing, which is used for curved, large and complex panels.
Recent advancements in additive manufacturing (3D printing) have revolutionised honeycomb insert production. 3D printing enables the creation of customised honeycomb designs with intricate internal structures.
Do you want to learn more about honeycomb inserts? Have a read of honeycomb inserts and their role in aviation!
Innovations in Fastening Technology
The integration of honeycomb inserts into military structures requires advanced fastening methods for structural integrity, but what are some of these innovations?
- Advanced Adhesive Bonding: Provides a seamless connection between honeycomb panels and other components. Adhesive bonding can also be used in marine applications.
- Mechanical Fastening Techniques: Uses specialised rivets and bolts designed for high-strength applications.
- Hybrid Bonding Solutions: Combines adhesive bonding and mechanical fastening for durability.
Quality Assurance and Certifications
Military-Grade Standards and Requirements
To ensure the reliability of honeycomb inserts in military applications, they must comply with strict military-grade standards. These standards specify requirements for:
- Mechanical Strength and Durability: Ensuring performance under extreme loads.
- Environmental Resistance: Protection against temperature fluctuations, moisture, and chemical exposure.
- Quality Control Processes: Verification of material integrity and manufacturing consistency.
Honeycomb inserts go through certification processes such as:
- Mechanical Property Testing: Evaluates compressive strength, impact resistance, and fatigue performance.
- Environmental Exposure Assessments: Tests resistance to extreme conditions such as heat, cold, and humidity.
- Operational Simulations: Assesses real-world performance in military scenarios.
Certified honeycomb inserts provide assurance that they meet the highest standards for military applications, ensuring reliability in combat and defence environments.
How Do You Choose Appropriate Honeycomb Inserts?
Choosing the right honeycomb insert depends on the following:
- What environment will you be operating in? Conditions such as temperature extremes, pressure variations, and exposure to chemicals.
- What are the load-bearing requirements?
- What are the impact resistance needs, such as the level of energy absorption required for ballistic or blast protection?
- What are the weight constraints, and do they compromise the strength?
- Are they compatible with other materials?
Design parameters for honeycomb inserts include the overall thickness of the panel, face skin thickness (rigid or plain), type of core, material or core or face skins, the fastener moulding compound, and whether it’s a flat, tapered or curved surface.
What about fastener styles? Engineers must consider:
- The size (or diameter) of the through-mounting member and whether it’s a bolt or a rivet
- Is it a through fastener or blind type?
- Should the installation be flush with the surface of face skin?
- Is a facing type or standoff head required on either end? What diameter and how thick?
- What are the torque requirements of the threaded type? Is a self-locking feature required?
- What material is needed for the fastener?
- What is the operating temperature of the installation?
- What are the design load requirements for each fastener?
- Is a moulded or mechanical fastener needed?
- What is the material compatibility with the mating fastener?
What are some expert recommendations?
Engineering experts recommend selecting honeycomb inserts based on the specific application. For example:
- Aluminium Honeycomb Inserts – Best for lightweight structural reinforcement.
- Aramid Fibre Honeycomb Inserts – Ideal for ballistic protection due to high impact resistance.
- Hybrid Composite Inserts – Suitable for applications requiring a balance of strength and flexibility.
Consulting with materials scientists and military engineers ensures the optimal selection of honeycomb inserts for mission-critical applications.
Case Studies of Honeycomb Insert Applications
One of the most notable uses of honeycomb inserts is in mine-resistant ambush-protected (MRAP) vehicles. These vehicles use honeycomb inserts in their armour panels for protection against explosive blasts while keeping weight minimal.
Honeycomb inserts are also widely used in:
- Military Aircraft, reinforcing fuselages and wings with lightweight, high-strength honeycomb panels.
- Naval Vessels, improving the durability of ship structures without increasing weight.
- Protective Gear and improving the performance of helmets and body armour.
Whether you’re looking for Click Bond Fasteners, GripLockTies, Hi Lok Tooling, Motorsport Fasteners, Space Fasteners, or aerospace tooling, AFT has a range of specialty fasteners that meet approved standards.
Needing Honeycomb Inserts? Order Online at AFT!
Honeycomb inserts are an essential component of modern military technology, and Applied Fasteners and Tooling supply the aerospace and defence industries with specialised fastening products and technical support.
Emerging as a leader in the industry and AS9120 quality certified in 2014, AFT works closely with only the most innovative fastener-related technologies and brands to push the boundaries of what is possible. We offer a personalised interaction and a value-added service for design, procurement, production, quality, maintenance and repair.
If you need custom product solutions, contact us today or shop in stock! We’re happy to give you an online quote if you have a specific order in mind.