The Benefits of Using Click-Loc Self-Locking Systems in Aerospace Applications
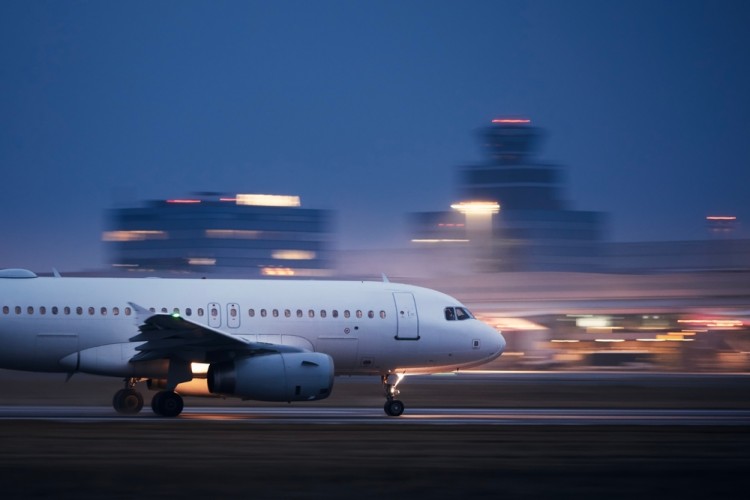
- November 22nd, 2024
- Categories: Uncategorised
Safety and lock wires have been used in aerospace for decades; however, this method is time-consuming, so an alternative was made.
The concept of Click-Loc was generated in response to a Pratt & Whitney U.S Air Force need for self-locking fluid fittings to replace the lock wire on the F119 engine.
A year later, Moeller Aerospace created Clic-Lok self-locking fittings, fasteners, fluid-fitting retrospect designs, and borescope plugs drastically improved this secondary locking technology, offering the same benefits without hassle for engineers using them.
The first Click-Lock self-locking borescope plugs were sourced for the GE90 fuel nozzle/manifold in 1992, and this technology expanded to turnbuckles, drain plugs, and more like the Boeing 777, Rolls-Royce engines, and Lockheed F-22.
But what are the advantages of Click-Loc in aerospace applications? This blog will explore their significance in the field.
Click-Loc Systems: What are They?
Setting a new standard for efficiency and safety in aerospace applications, Click-Loc has replaced traditional methods in The Air Force, Army, and other military branches. This introduced self-locking to vehicles, aircraft, and weapons. So, what are Click-Loc systems?
In aerospace, everything must be installed correctly. Click-Loc has its own built-in secondary locking feature, which eliminates safety wire cotter pins and any other form of secondary locking feature!
As an innovative and time-saving alternative to anti-rotation applications (lockwire, safety pins, or cotter pins), Click-Loc is simple to install, doesn’t need maintenance, provides full life cycle reliability in areas with high vibration and is critical to mission success. It does this by having fingers actuating over a cam pattern that provides a positive force on threads to ensure there is no failure.
Click-Loc is commonly used in aircraft engines, as well as in industrial, space, marine, and military industries. All in all, it is a small device with significance.
There have been no reported failures of Click-Loc in over 20 years in any severe applications.
What is the Antique Lockwire Method?
Safety wire (also called locking or lock wire) has been standard for securing fasteners on aircraft.
Winding thin, flexible wire around nuts, bolts, and components prevents them from loosening due to vibrations, mechanical stresses, or temperature. Lockwire, however, is brittle and can break off, increasing the risk of foreign object damage (FOD). It is time-consuming, tedious, and requires complex wiring procedures. Frequent inspections are also necessary to ensure the lock wire stays secure over long periods.
Advantages of Click-Loc Systems
Why has Click-Loc patented self-locking technology developed? It addresses the limitations of safety wires by providing projects such as aircraft with a powerful, reliable, and reusable solution. Let’s look at its advantages!
1. Enhances Operational Efficiency
Click-Lok products offer a 100% positive locking mechanism that never loosens during operation, even in demanding environments like high altitudes. They have been tested to handle hundreds of assembly and disassembly cycles without fail, setting a new standard for safety. How have they been used in the aerospace industry as a successful application?
- It has been used on engines such as the EJ200, GE F110, F135, GE38, and the PW1000G.
- Major manufacturers such as Lockheed Martin used these self-locking fasteners for the F-35, and Blue Origin used self-locking plugs!
- A U.S Air Force contract was issued for Click-Lock self-locking fluid fitting retrofit of F110-100 engines to address leaking fluid fittings
- In 1999, Click-Lock self-locking borescope plugs were found by Rolls Royce for EJ200 engines
- The U.S Army chose Click-Loc self-locking fluid fittings for the Crusader Cannon cooling system
- The Click-Loc self-locking fastening system was used by Lockheed Martin in 2013 to replace lockwire in an ergonomically complex location on F-35 weapon pylons
- Pratt & Whitney signed a 100-year agreement with Click-Loc in 2021 for borescope plugs on the GTF engine family
2. Innovative Design Features
With over 250,000 parts produced and over 1 billion flight component hours, what are some of the design features of Click-Loc?
Self-locking fasteners
- Inconel material
- Operates in temperatures up to 600 degrees Celsius
- Sizes are customisable
- Applications include turnbuckle fasteners, nut and bolt assemblies, bolt and washer assemblies, bearing lock nuts, retaining nuts, pylon nuts, lockrings, adjustable rod ends, Heim joints, hydraulic connectors, and rod end adjusters
Self-locking plugs
- Inconel material
- Operates in temperatures up to 600 degrees Celsius
- Customisable sizes to choose from
- Applications include engine access/inspection ports, borescope plugs, drain plugs, or sensor applications
Self-locking fittings
- Inconel material
- Operates in temperatures over 600 degrees Celsius
- Tube sizes are -03 through to -16 and are customisable
- Applications include gas fittings, gas couplings, fluid fittings, fluid nozzles, hydraulic hose fittings, fluid flow systems, test stand fittings, and fluid transfer systems
The Bolt and Washer Locking System has a robust application retention system to secure heavy loads and is scalable for alternative-sized applications. Likewise, the Turnbuckle Fastener System is a secondary locking device that secures the turnbuckle, maintaining length and guaranteeing no back-off.
3. Material Quality and Durability
Inconel is one of the most common alloys in aerospace components (such as rocket engines, nuclear reactors, and turbine blades) due to its oxidation resistance, creep properties, and superior mechanical properties.
- Considered a superalloy, Inconel can be used permanently above 600 degrees Celsius
- Highly resistant to fatigue, Inconel 718 accounts for half of the weight of aircraft turbojet engines, the main component for discs, blades, and the casing of the high-pressure section of the compressor and discs, as well as some blades of the turbine section
- Inocel is also used in several applications in cryogenic environments and rocket engines since it is tough in low temperatures or preserving parts from brittle fractures
- Inconel contains a large amount of iron, and due to its low mobility and kinetics, reduces its susceptibility to post-weld cracking
- Alloying elements in Inocel (such as nickel) combat chloride-iron stress corrosion cracking and protect from corrosion
4. Weight-Saving for Aerospace Applications
Click-Loc self-locking systems are lightweight fastening solutions! What are some examples?
- Click-Loc is made from lightweight materials such as titanium or high-grade aluminium alloys, contributing to high strength yet minimising weight for aerospace operations
- A self-locking feature like Click-Loc eliminates the need for extra locking components such as washers, safety wires, or locking tabs. This lowers the weight of the fastening system
- Click-Loc evenly distributes load, so there’s no need for additional structural reinforcements
- Click-Loc is designed specifically for weight-sensitive aerospace environments
5. Meets Quality Standards
Click-Loc is committed to essential quality standards for critical components, meeting ISO 9001:2015, ISO 14001:2015, and AS-900D certification. It is also:
- Compliant with GE S-1000, PW QA-6076, and MIL-Q-9858A
- FAR 33 certifications for GE, Rolls Royce, and Pratt & Whitney
- REACH compliant and does not contain any SVHCs
- NADCAP is accredited for Chemical Processing (Dry Film), Non Conventional Machining (EDM) and Non-destructive Testing – FPI
Click-Loc VS. Lockwire: What’s the Difference?
Instead of threading and twisting, Click-Loc clicks and locks into place. Instead of modifying a standard lockwire product to suit your project, Click-Loc is designed and tailored to you. Let’s look at some clear differences:
- Click-Loc is more resistant to vibrations, stress, and extremely high temperatures
- The self-locking devices of Click-Loc can easily be refitted
- Click-Loc offers torque retention with no back-off
- The self-locking technology of Click-Loc is reusable and reduces the risks of FOD from safety wire
Are there any advantages to Lockwire?
- When putting together lockwire, it takes a lot of time and skill to do so
- Designed to prevent the loosening of nuts, bolts, and other fasteners that hold systems together, lockwire requires manual threading of hard gage wire together through two or more fasteners
- Two strands of wire need to be twisted in a double-twist configuration, and this safety wiring prevents the fastener from loosening when tightened
However, each process step is more prone to human error as engineers must know how to twist and thread lockwire properly. Compared to Click-Loc, it can only be used once before being thrown away.
Whether you’re looking for self-locking nuts or specific aerospace fasteners to support life cycle costs, AFT offers custom solutions for secure locking in harsh environments.
Aerospace Fasteners: Choose Applied Fasteners and Tooling for Click-Loc Solutions!
For design interchangeability, quality, and design technology such as strong tensile strength, torque control, a unibody beam spring, and a self-locking feature that is always engaged, AFT has emerged as a leader in the fastening system supply chain.
Registered and AS9120 quality certified in 2014, we push the boundaries of what is possible for innovative fastening technologies. Offering a personalised interaction and value-added services in technical support for a range of markets, AFT supports you through the design, procurement, production, quality, maintenance and repair.
From Avibank Ball Lok Pins to Hi Lok Fasteners, we have Cherry Tooling, Countersink Tooling, Cable Tie Mounts, Motorsport Fasteners, Specialty Fasteners, and more! Contact us today to Shop in Stock!