Common Mistakes to Avoid When Using Aircraft Tools
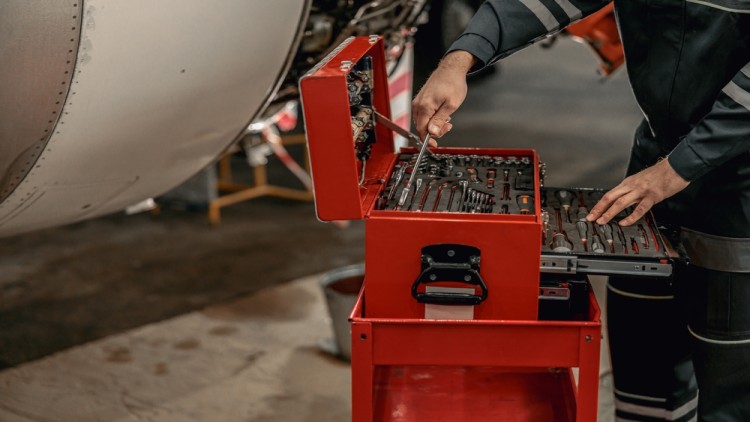
- October 01st, 2024
- Categories: Uncategorised
In the aviation industry, tooling is critical for various procedures, as well as regulatory compliance and the overall safety of engineers, pilots, and flight passengers.
A single mistake can have detrimental consequences –such as the well publicised Boeing 737 incident–so engineers must use aircraft tools correctly and adhere to strict safety standards!
This article will explore the common mistakes to avoid when using aircraft tooling, how to stay safe during a project build, and how to ensure the safety of the aircraft when and after it takes flight.
Importance of Tool Maintenance
Aircraft–such as commercial and private jets–all require periodic maintenance to function. If there’s even one screw out of place, it could affect your flight.
For example, an aircraft’s engine mount and exhaust system can develop corrosion and wear over time (no matter how durable the material may be!), so it’s important to observe these problems with the right tools. Not taking the steps to maintain them can result in expensive failures.
So, why is tool maintenance so critical?
During the aircraft maintenance process, every single aircraft part must be installed correctly and operate without any technical faults. You don’t want to end up with missing parts or maintenance mistakes, such as fuel pipes not being fitted, bolts drilled wrong (not adhering to the right tension), Fire Control Units not being fitted, and many others.
Proper maintenance of tools reduces the risk of accidents and ensures that maintenance procedures are being executed properly.
What are some causes of maintenance mistakes?
> Fatigue. An aerospace engineer may have been awake for 18 hours, so it’s important to set maximum duty day limits and rest periods.
> Distractions. Limit distractions when maintenance personnel are working on aircraft. Policies and procedures should limit phone calls and pull personnel away from tasks during maintenance.
> Staffing. A high workload with little staff can increase the risk of tool maintenance errors. Staffing must consider scheduled maintenance.
Aircraft Tools: Mistakes to Avoid
Aircraft safety issues can be complex, but what mistakes should you steer clear of as an aerospace engineer?
Not Selecting Appropriate Aviation Tools
With any aerospace project, it’s mandatory to have a solid understanding of tool specifications and how to match the right tools to the task. For example, are you working on a mainframe, an engine, or the electrical wiring, and what material or tooling is safe to use?
How do you choose the right tooling components?
> Material durability and compatibility. Each material has unique properties (for example, titanium has an excellent strength-to-weight ratio), so it needs a specific tool for shaping and machining. Picking the wrong tool can result in tool failure, excessive wear, and compromise part quality. A good example is high-strength alloys, which can withstand high stress and are ideal for load-bearing components.
> Consider precision and tolerance requirements. Even the slightest deviation can impact aircraft performance, safety, and how reliable it will be. Always think about environmental impacts and dimensional tolerances.
> Safety and ergonomics. An ergonomic tool reduces the amount of physical strain on the operator, so grip comfort, weight distribution, and adjustable components must be a priority. Choose materials that are non-conductive, corrosion-resistant, and durable, adding surface treatments or coatings to cut the risk of slipping.
> Weight. When putting together an aircraft (whether it be a spaceship or a smaller plane), aerospace components must be lightweight and handle the forces/stresses during flight.
Incorrect Training and Familiarity
The cost of failure is high in aerospace, so taking all measures for effective oversight and control is essential. Part 147 of the Civil Aviation Safety Regulations 1998 (CASR) sets out the requirements for maintenance training organisations, individuals requiring licenses and ratings for the performance of maintenance certifications, and certificates of release to service for aircraft maintenance.
For example, appropriate awareness of the calibration program needs to be fully documented and understood throughout an organisation’s technical personnel. Proper training with tools can include:
- Understanding the processes that drive effective management of a Part 145 Compliant Tool Store
- Understanding the processes of managing documentation related to airworthiness, tooling, and calibration control
- Understand the principles of Electrostatic Inspection
- Be confident in full compliance within the supply chain and being able to develop and improve the tooling store
- Annual and period tool inspection
- Understanding Foreign Object Debris (FOD)
AC-147-01 includes Legislation on Practical Consolidation Training (PCT), which is one way of satisfying the practical component of aircraft type rating training for B1 and B2 LAME licenses.
It is also important to keep up with tool developments, such as ClickBond fasteners and Perfect Point Edrill to learn more about new innovative tooling in the industry.
Reach out for personalized support and innovative solutions for your aerospace and defense projects.
Ignoring Tool Organisation and Safety Protocols
You don’t want to misuse a drill when constructing or maintaining an aircraft! Always review risk management practices and procedures such as Policy 221 – 13 outlines Tool Control and Accountability, which is to reduce or eliminate aircraft incidents or accidents, including loss of life or damage to equipment. What are some of the responsibilities?
- All AOC personnel must make sure that tool control practices and accountability guidelines are accomplished in accordance with this policy
- Supervisors must inspect all inventoried toolboxes and PMEL at least annually so tools are serviceable, accountable, and calibrated. QA or the designated Tool Box Monitor needs to accompany the supervisor
- Tools must be marked in an acceptable manner that allows for easy source identification. Acceptable aviation methods include colour coding, etching, shadow boxing, shadow boards, tool counters, tool tags, Employee Names, and more.
- All tools intended for use in, on, or around an aircraft shall be accounted for and permanently marked for identification to indicate the toolbox it is assigned to
- NOAA personnel should only use government-issued tools to accomplish work. Personal tools are prohibited on or around aircraft. However, contractors may use their own tools under Section 3.8.
- All tools must be accounted for at the beginning and end of daily work shifts, ground or flight tests, and at the completion of work and are returned to the appropriate toolbox when leaving the work area. Tools will never be left unattended in the aircraft except for short periods, such as a lunch break
- Visiting personnel such as engineers, technicians, or contractors that are required to work on a NOAA aircraft shall have an AOC sponsor, which is chosen by the appropriate Branch Chief
- For Lost and Found tool procedures, any time a tool or personal equipment is lost on or around an aircraft, all activity will cease in the affected area, and a search will be initiated
- Tools or equipment requiring calibration/certification in accordance with 14 CFR 43.13 must be calibrated through the MacDill AFB PMEL, appropriate vendor, or qualified AOC personnel
Never rely on an improvised solution; check out our quick guide to selecting the right aircraft repair tools for your needs.
Misusing Aircraft Tools
Misusing an aircraft tool can be dangerous for the user and cause problems for the aircraft structure. What are some safety rules you need to adhere to?
As a general rule of thumb, the Occupational Health and Safety Administration (OHSA) recommends that all tools be kept in good condition with regular maintenance scheduling, that the right tool be used for the work at hand, that each tool be examined for damage before use, that tools be operated in accordance with the manufacturer’s instructions, and that the right personal protective equipment be used.
Hand Tools
Misuse and improper maintenance can cause injury or hazards when using hand tools. For example, if a chisel is used as a screwdriver, the tip of the chisel can break and fall off, injuring a user or other employees.
Rivet sets have mushroom heads and have the potential to shatter from impact and send sharp fragments flying! Whenever using cutting tools such as saw blades, ensure they are sharp.
Iron or steel hand tools can produce sparks that are dangerous around flammable substances, so when working in a fire-hazard area, spark-resistant tools made of non-ferrous materials should be used.
Power Tools
Including electric and pneumatic tooling, aerospace power tools need to be used with caution and proper training.
Tools must never be carried by a cord or hose, keep hoses and and cords away from heat, oil, and sharp edges. Disconnect tools when not using them – before servicing and cleaning them – when changing accessories, secure work with clamps or a vice, avoid accidental starting, and follow instructions in the user manual. Safety guards must never be removed when a tool is being used, as this protects operators from moving parts, high-energy systems, and other components.
Electric Tooling
Serious hazards can occur from electrical tooling, such as electrical burns or shock, so you need to have proper training before using them.
To protect yourself, electric tooling must have a three-wire cord with ground and be plugged into a grounded receptacle, double-insulated, or powered by a low-voltage isolation transformer.
Operate electric tooling within their design limitations, store electric tools in a dry space when not in use, do not use electric tools in damp or wet conditions unless approved, and ensure that cords from electric tools do not present a tripping hazard.
Pneumatic Tooling
Pneumatic tools need to be fastened securely to the air hose to prevent them from becoming disconnected. If an air hose is more than 1/2 inch in diameter, a safety flow valve needs to be installed at the source of air supply to reduce pressure. These precautions need to be taken with an air hose recommended for electric cords because the hose can
Likewise, when using a rivet gun or air hammer, you can install a safety clip or retainer to prevent the set from being ejected when in use.
To avoid these mistakes, it’s important to adhere to safety guidelines, potential hazards posed by the tools, and pay attention to the surrounding work environment.
Reach out for personalized support and innovative solutions for your aerospace and defense projects.
Types of Aerospace Tooling
What type of aerospace tooling can you use to enhance the durability of your next project?
Jiffy Tooling
Jiffy Air Tools created the “Modular Tool” for drill motors and attachments (JMD), Jiffy Motors has a wide variety of drill attachments. Engineers can use Jiffy drilling and assembly tooling from drilling units in addition to spares and consumables.
Atlas Copco Drills
Atlas Copco Drills provide consistent reliability and performance. The LBB / LBP / D21 pistol has superior ergonomics and productivity. The drill is equipped with a rubberised pistol grip that reduces temperature differences.
Cherry Tooling
Cherry Tooling is manufactured by Cherry Aerospace, which has been specified and used by aircraft manufacturers and repair facilities worldwide for over 60 years. Cherry Installation Tools can be used in a variety of hand, pneumatic, and pneumatic/hydraulic versions.
Rivnut Tooling
Rivnut tooling can combine air hydraulic flaring and manual unwinding, setting alloy and steel rivnuts without high air consumption. It is used in aerospace, where a thread may be required for steel and alloy sheet panels, fiberglass, and timber board, where welding isn’t an option.
If you would like to learn more, have a read of understanding the different types of aerospace drills!
Invest in Aerospace Tools at Applied Fasteners and Tooling
Enhancing industry and defence, Applied Fasteners and Tooling has emerged as a leader in the fastening system supply chain.
Registered and certified to AS9120, AFT is recognised by the Victorian Defence and Space Network, offering innovation for fastener technologies and companies, pushing the boundaries of what is possible.
Whether you’re looking for GripLockTies, Drilling Equipment, Motorsport Fasteners, Cable Tie Mounts, Hi-Lok Tooling, or Countersink Tooling, we offer a personalised interaction and value-added service from the product life cycle to design, procurement, production, quality, maintenance, and repair. Request a quote and contact us today for custom solutions!