Understanding the Different Types of Aerospace Drills
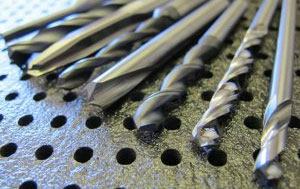
- August 12th, 2024
- Categories: Uncategorised
If you work in the aerospace industry, it is critical to use the correct types of aerospace drills for your project. The Aerospace Industries Association is responsible for creating and maintaining part standards for aerospace parts and components within the AIA’s National Aerospace Standards (NAS) library.
When using drill bits, you may come across descriptions such as “Type B”, “Type J”, or “Type C”–each meeting national standards NAS907, NAS937, and NAS965–but what high-speed steel should you use for your operation?
Aerospace drills aren’t like the hand drills you would use at home. They are specialised tools designed to meet the demands of the aerospace industry. With the correct drill, you can achieve accurate hole-making in important aerospace components where precision is non-negotiable.
Let’s look at how aerospace drills are used, drill types and their uses, and why they are so critical to the building blocks of aircraft, both commercial and for outer space.
Aerospace Drilling: An Overview
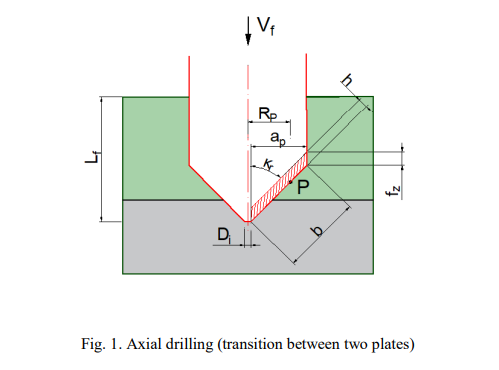
Metal-composite hybrid structures are essential for aeronautical construction to maintain their mechanical properties. Due to differently assembled materials (which have distinct machinability), the right drilling tool is critical when building, repairing, or maintaining an aircraft. This is especially the case for commercial flights or space missions, which need the strongest materials on earth for safety.
Let’s look at smart drilling. Why is smart drilling for aerospace state-of-the-art? Thousands of holes need to be drilled to assemble aeroplanes, and smart drilling is key to maintaining high performance in the air. The use of smart manufacturing (SM) in the drilling aerospace industry is based on real-time monitoring for adapting parameters, live streaming real-time data from the tip of the drill bit to the joystick on the driller’s chair.
Likewise, the need for cleaner energy is an important challenge for the aerospace industry. Their weight restricts hybrid and electrical aircraft’s autonomy, so weight reduction in transport systems such as aircraft can have a positive impact on carbon emissions. In many cases, the materials used for aircraft are aluminium alloys, titanium alloys, and CFRP, such as polymers and carbon fibre.
A monitoring tool force and power can identify the cutting material during drill stack composites for aerospace, and controlling this tooling process improves tool life, manufacturing productivity, and tool quality for aerospace engineers, who need to be aware of their torque, forces, power, and cutting speed.
What about manual drilling?
Providing operational advantages, flexibility, precision, and reliability for drilling holes, aerospace engineers can take advantage of an ergonomic tool. A modern aircraft has approximately 3 million holes, and 750,000 of these are manually drilled, accounting for 25% of holes drilled. Semi-automated drills account for 45% of the total, and fully automated drills account for 30%.
How is a manual drill used? A trigger, lever, or button activates the drill’s motor, which can be powered by electricity or pneumatic pressure, ensuring a consistent, uninterrupted performance. The engaged motor generates a rotary motion, allowing the drill bit to penetrate the material. By adjusting the torque and speed settings (using the drill’s gearbox) the drilling process can suit the requirements of the user.
To learn more about specific drill types, read about the E-Drill 2.0 System vs. Hand Drilling in the aerospace industry, which discusses manual drills and the electric drill, which can better suit some aerospace applications!
Drill Types Used in Aerospace Applications
Drill types “B”, “C”, and “J” are creations of The National Aerospace Specification Committee, which is a subset of the Aerospace Industries Association (AIA), and these parts meet the standards for high strength, close tolerances, and acceptable testing for the aerospace industry.
Angle drills (Pork Chops)
Also known as Pork Chops, angle drills are used daily for a wide range of aerospace applications, as well as oil fields and refineries.
- Right angle drills are carefully designed for high level operation conditions, such as aerospace, engineering, and material removal applications.
- These drills allow engineers to work in tight spots, such as for aircraft repairs and mechanical maintenance. The powerful motor delivers high speeds and torque.
- The angle head is reinforced for stronger durability, with a 45 degree, mini 90 degree, 360, and a compact or heavy duty 90 degree angled version.
- The high-precision drill capability accepts standard threaded bits to eliminate chuck slippage.
- A built-in regulator can easily adjust speed within tool capability.
- It has a special built-in silencer, reduces noise, and isn’t a work hazard during operation.
Atlas Copco Drills
Atlas Copco drills offer aerospace solutions for assembly, material removal, and quality assurance. Let’s look at some of Atlas Copco drills models and how they can help.
- The pneumatic handheld drill LBB16 is small, low weight (600g), high power, and has perfect ergonomics with rubber handles.
- The modular offset head drill is optimal for aerospace production, a small-sized tool perfect for access to cramped, limited spaces.
- The battery pistol grip nutrunner tensor STB offers mobility and accessibility. You can partner this model with a Power Focus controller for accurate torque monitoring and joint traceability!
- The vibration-damped riveting hammer RRH minimises the operator’s exposure to vibration while maintaining high tool performance.
Drills Pneumatic
From generic handheld drilling units from manufacturers such as Desoutter, let’s look at different types of pneumatic drills and how they can help.
- ZT677/ZT777 high speed angle drill attachments are designed to run at any speed up to 6,000 rpm in the tightest and most demanding applications, ideal for metallic, graphite, and composite materials used in the airframe industry.
- The Desoutter DR750-P6000 pneumatic drill has an RPM of 6,000, with a high feed force for effective drilling. It includes an ergonomic shape, single and double-handed use, and is ideal for industrial drilling applications.
- Lubbering L.AUD pneumatic drills can be individually configured thanks to its modular structure, the basis machine is together with the locking system ready to use and includes right-angled, inline, grip models and motor types (55, 56, and 57) available.
Jiffy Tooling
Jiffy Tooling offers drilling and assembly tooling for aerospace.
- The Jiffy Air Tool–such as modular tool platforms–is a platform for drill motors and attachment. It is forward running, reverse running, and reversible, offering 250 – 20 000 RPM, a pistol grip style available in various thread sizes.
- Torque control straight hi-lok motors are designed for fasteners requiring a precise yet repeated torque with minimal torque reaction. All models are tested to Six Sigma toque standards.
- Aviation grade angle nutrunners include torque ranges from 18-400 in-lbs. They are adjustable shut-off clutches that provide precise torque and feature a soft grip over mould that offers comfort while reducing grip force.
For more information, have a look at the Jiffy 2022 pamphlet!
The Aerospace Drilling Process
What are the drilling processes and strategies used in aerospace?
- Conventional axial drilling is the most common process for machining of fastening holes in the aircraft industry, which is also known as ‘conventional drilling’.
- Monitoring the tool wear. This ensures the quality of the hole drilled, controlling the diameter, burr, and the surface roughness.
- Vibration-assisted drilling (VAD) based on the addition of oscillations to the feed motion of the tool. Ensuring chip fragmentation and easing its evacuation, this drilling process is reliable for multi-material stacks even if cutting conditions remain.
- Drilling metallic alloys (such as aluminium and titanium) together with composite fibre laminates and other drilling processes have been developed to combat issues such as keeping the same tool and cutting conditions.
Cutting power and forces of axial drilling
In homogenous material, the cutting force is determined experimentally for a pair tool-workpiece. It is a function of the cutting depending on the range of the cutting material influences for a given tool. The cutting force (MPa) can be calculated using the cutting force for a single cutting edge. If the uncut chip thickness is constant, the chip load area is the feed per tooth multiplied by the axial depth of cut a.
In some cases of axial drilling, the cutting force will be integrated along the cutting edge and will have two materials. This transition is used in data processing as a trigger for identifying a new material, and as soon as the signal is stabilised, new parameters are calculated and the cutting speed and feed are updated into the program.
What about orbital drilling?
Unlike axial drilling, orbital drilling doesn’t have vibration assistance, and the cutting edge isn’t simultaneously in contact with the workpiece. The cutting force and power depend on the cutting process geometry, and orbital drilling is a circular milling process with vertical displacement.
These active cutting edges depend on the radial depth of cut and the relation between drilled diameters and nominal diameters.
In the case of a transition between two materials, the different materials affect the parcel or two cutting edges, which is why the rough signal from power or cutting force cannot be used for direct identification and fine data treatment is needed for the trigger.
What are the most common features of aerospace drills?
- They’re made from high-strength materials, such as premium carbide, to handle the extreme demands of aerospace machining.
- Aerospace drilling handles precision cutting, producing clean, accurate holes with minimal burrs.
- There are multiple flute configurations to increase the performance of materials and cutting conditions.
- They come in specialised designs, such as split points and parabolic flutes, to support chip evacuation and reduce thrust forces.
- There are many custom options to meet aerospace requirements, so every application will have a specific tool!
Industrial applications include aerospace manufacturing for airframes, wings, or other structural components, spacecraft construction–such as precise holes or engine components–drilling through composite materials for modern aerospace applications, and accurate drilling operations for aircraft maintenance and repairs.
Are you searching for high-speed steel, air drills, a pneumatic drill, a drill chuck, drill stops, or drill bits specific to your upcoming project plans? AFT has dozens of fasteners and tooling for many defence-critical markets and applications that meet Quality Assurance Procurement Requirements. Shop in stock today.
Aircraft Repair Tools: Request a Quote at AFT!
With many renowned brands and a reputation for product innovation in drilling equipment, AFT was registered and AS9120 quality certified in 2014, founded to supply the aerospace and defence industries with specialised fastening products and technical support. Offering customer products and solutions, we are depended on by customers as a reliable partner for exceptional quality and delivery.
Emerging quickly as a leader in the fastening system supply chain for Speciality Fasteners, Cable Tie Mounts, Motorsport Fasteners, Honeycomb Inserts, EMI/RFI Shielding, and aircraft tools, we always push the boundaries of what is possible.
Whether you need support on types of drill bits, a power drill, an air compressor, solid carbide drills, a handheld drill, or drills powerful enough to create larger holes or handle stainless steel, contact us today for a quote and we can guide you on the best tooling and consumables for your industry.