What Are Nut Plates and Their Uses in Aerospace Applications?
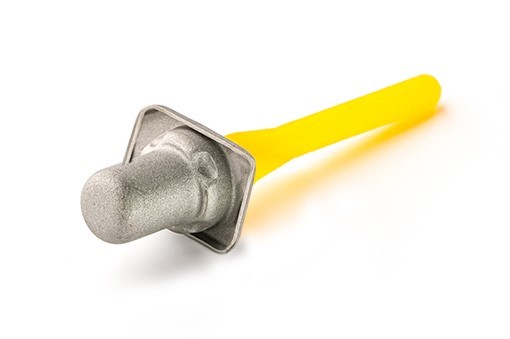
- August 16th, 2024
- Categories: Uncategorised
If you really want to be well prepared for an aerospace project, you need to make use of the correct fasteners and tooling for high-accuracy applications such as aircraft structures and sheet metal.
When a joint needs to be removable–and Hi-Lok fasteners just don’t cut it–a nut plate is used. These self-locking, self-wrenching nuts are used in constrained areas to offer a permanent nut element inside a fatigue-critical joint where bearing stress is concentrated. This can support a fairing, access panel, or other element to be attached with a screw.
This article will detail the purpose of nutplates in the field of aerospace, their crucial role, and why they are beneficial. After all, every small component matters.
What are Nut Plates in Aerospace?
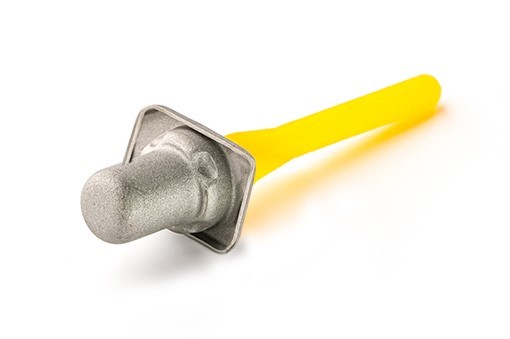
Aeroplanes are built with nut plates, which consist of a built-in nut and a supporting anchor frame. Otherwise known as plate nuts, anchor nuts, or captive nuts, they are used with a threaded bolt or similar type of threaded rod, and most nut plates feature a triangular shape.
Two ends on the sides have an unthreaded hole, whereas the end in the centre has a threaded hole, which is designed to support a threaded rod or bolt. This bolt can then be twisted into the threaded hole of a nut plate. Designs can either be fixed or floating.
In the case of fixed plate nuts, the plate and the nut are integrated, whereas floating plate nuts involve a nut being attached to the plate. The plate contains one large hole and two smaller holes; the larger one is used for screw installation, whereas the two smaller holes with a diameter of 2.38mm help to mount the plate nut onto a component.
What are the primary features of nut plates, and what do they do?
- Nut plates are available in alloy steel, A286, and titanium.
- Available finishes include silver-plated, cadmium-plated, passivated, solid film lubed, and HIT-KOTE 4NC coating.
- Nut plates include a captive or removable nut element.
- Nut plates have a radial float of up to .150″ (3.81mm)
- They have high vibration resistance.
- They have self-locking torque deliver up to 25 cycles, or up to 1500 cycles for some special applications
- Nut plates have internal threading, whereas bolts and rods have external threading.
How do you configure nut plates? It depends. The dimensions, materials, configuration, and coatings vary based on the environment and application area.
For example, the nut plate used in the Cargo hold of the Boeing 737-300 has the part number BACN10JR3F. This part number details indicate that the nut plate is double-sided floating with a threaded standard of 1900-32 UNJF-3B, made from steel, and coated with cadmium.
How Are Nut Plates Installed?
Although Nutplate Tooling (such as pneumatic spacematic drills) supports a threaded rod or bolt, nutplates are installed using a different type of fastener: rivets, which are mechanical fasteners used to join multiple parts. Let’s look at the installation method for nutplates according to Clickbond!
Step 1: Substrate is Cleaned
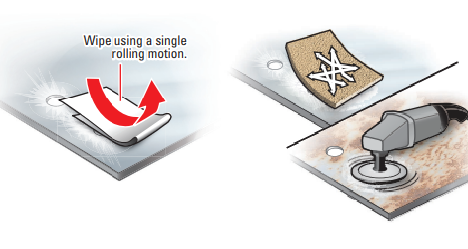
The substrate is cleaned to remove all surface contaminants. A clean, lint-free cloth and fresh cleaning solvent (CB911 or acetone is recommended) are used. The cloth is saturated with solvent, and the substrate is wiped with a single motion.
An abrade substrate is used on the installation part, such as Composite 160-180 grit or Metallic 120-180 grit. The cleaning process is repeated to remove abrasion residue.
Step 2: The Part is Prepared
A solvent wipe is used for the nut plate base with a single rolling motion to remove residue. The adhesive is evenly applied.
Step 3: Adhesive Bonding
An installation fixture pulls a nut plate into place, aligning it securely against the surface. The adhesive squeeze-out is visible around the base of the part.
Step 4: Curing and Completion
The adhesive is left to cure. Adhesive isn’t wiped or disturbed during this period of curing. Once the adhesive has been cured, the installation fixture is removed.
Rivets play a part in the installation process. Instead of an external threading, rivets feature a smooth body with a head on one end and a tail on the other.
These rivets are put through unthreaded holes, and the tail is deformed, so they stay in place. Depending on how the tail is deformed, it can expand nearly 1.5 times its original size, meaning that the tile will wrap around the underside of the hole where the rivet is placed.
A single rivet is often placed through each of the two unthreaded holes. Most nut plates are installed with rivets, but they still support a threaded bolt or road in the centre.
Rivets offer advantages over threaded fasteners as threaded can loosen when exposed to vibrations. On the other hand, rivets are resistant to loosening as they don’t have external threading.
Importance of Nut Plates in Aerospace
According to this Fastener Design Manual by the EAA, nut plates (another word for them being anchor nuts) are usually used on materials too thin to tap, installed where access to a regular hex nut with a wrench would be difficult, if not impossible. Since their installation is expensive, they are primarily used by aerospace companies, but why are they so important within the aerospace field?
Nut plates being used–in some cases–are the only way to complete installations. What are some affected/problem areas that these nuts can solve?
- The installation of antennas.
- Propeller spinner or bulkhead
- The attachment of wing root fairings.
- Instrumental panel installation.
- Cowling attachment.
- Installation of accessories on the firewall.
- Inspection over covers and hatches.
Substituting anchor nuts in these locations not only makes the installation possible but also allows engineers to remove the part later for maintenance or replacement.
How do you select the ideal anchor nut? Most anchor nuts are suitable for an aerospace job. However, it needs to be the correct size for the bolt or machine screw to be installed. If the wrong size nut is installed, this can mean extra unnecessary work needs to be drilled out and replaced. Often, it isn’t uncommon for an all-metal homebuilt to have more than 300 anchor nuts installed!
Two of the most common varieties are the two lug nylon insert locking type (AM366F), and the two lug all-metal anchor nut (K1000), but always check your supplier catalogues for options and sizes.
Types of Nut Plates
Aircraft anchor nut plates
These nut plates are used in the aircraft, aerospace, defence, and electronics industries and are useful in blind locations where an attached nut needs to be frequently removed for inspection and maintenance.
Self-wrenching and offering positive positioning of the bolt, nut mounting lugs can be riveted, mounted, welded, or screwed to a structure.
Fixed nut plates
Designed for blind-mounted applications in aerospace where using hex nuts can be problematic (or where using an attached nut is desirable), this can improve the maintenance process.
Fixed nut plates can be made from alloy steel or carbon steel, with finishes such as cadmium plates. If you’d like to find a specific size in your industry, AFT is a leading supplier of aircraft fasteners
High-strength nut plates
High-strength nut plates are beneficial for aircraft and aerospace in terms of improved durability, weight reduction, added structural integrity, and lower total assembly costs.
These nut plates are as slow as 1/5th the weight of conventional anchor plates, have higher proof-load performance than a conventional design, have free-floating characteristics available for self-alignment with bolt if desired, self-retention features available for easy assembly, and pre-tapped for inexpensive thread cutting screws.
Floating nut plates
Low-profile and lightweight plates and floating nut plates can install a captive nut behind a panel.
This nut plate type supports an assembly that isn’t perfectly aligned for an engineer to work with. Floating nut plates can be made from iron alloy, carbon steel, or steel with corrosion resistance. Floating finishes can include cadmium plate, silver overall, and dry lubricant.
Open and capped nut plates
The majority of nut plates are open, so they have a threaded hole in the centre that does not feature a back.
However, capped nut plates still have a threaded hole, but they do feature a back. Choosing a capped nut plate means engineering don’t need to stress about a fastener or bolt damaging adjacent parts.
Do you need guidance for your aerospace mission? Whether you need riveted nut plates, a washer head, structural bolts for military aircraft, or innovative fasteners, AFT can support you with critical applications.
Applied Fasteners and Tooling: Aircraft Repair Tools for Aerospace Applications
No engineer wants an amateur-built aircraft and nut plates strengthen the sheet metal from external forces.
Emerging as a leader in the fastening system supply chain, Applied Fasteners and Tooling was registered and AS9120 qualified in 2014, founded to supply the aerospace and defence industries with specialised fastening products and technical support.
Whether you’re looking for Cable Tie Mounts, Hi Lok Fasteners, GripLockTies, Ball Lok Pins, Motorsport Fasteners, or spacecraft fasteners that meet Approved Standards, we have a wide range of aerospace consumables!
We support the product lifecycle by working with design, procurement, production, quality control, maintenance, and repair. Responsive, collaborative, and professional, we push the boundaries of what is possible. Contact us today and shop in-stock quality brands.