What Is Better for Navy Environments – Bonding or Welding?
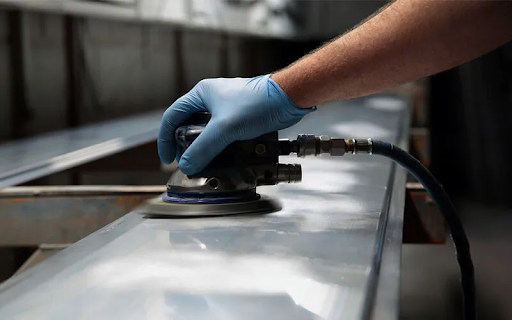
- December 14th, 2023
- Categories: Uncategorised
Choosing between bonding or welding can make a major difference to the quality and durability of your future design. If you’re a metal fabricator in the navy industry, a strict set of specifications must be met, including structural integrity, safety, and structural degradation.
Manufacturing processes also depend on the structure’s geometry, loading conditions, corrosion, and material properties. Whether you’re looking for effective methods to design steel alloy ships or larger-scale tests on marine welding projects, bonding and welding both have their advantages.
With this in mind, what is the recommended approach? Throughout this article, we’ll detail the key differences between bonding and welding, including their use in the construction of naval materials.
Differences Between Panel Bonding Adhesive and Welding
Adhesive bonding and welding are different methods used by naval architects. Bonding involves an adhesive to seal two pieces together, whereas welding involves melting the edges of panels and fusing them together with heat and filler material.
How do these processes compare? Let’s assess both across a range of different criteria.
Strength and durability
Although both welding and adhesive bonding are durable, the method used depends on the materials joined, the skill of the architect, and the use of the final product.
Welding can fuse strong panels, whereas adhesive bonding can distribute the stress of materials evenly, which helps if high stress is a concern.
Ease of use
Adhesive bonding is generally easier than welding. It generally involves cleaning the surface, applying adhesive, and piecing panels together. Welding, on the other hand, requires controlling heat by experienced welders, handling welding equipment, and managing a filler material. Usually, on ships, a fire watch person is required in case of fire while welding.
Appearance
Adhesive bonding often has the advantage in terms of appearance. Bonding can create a seamless finish without heat-affected zones being visible. Welding creates a small line where the panels have been joined.
Cost comparison
In terms of cost, with today’s labour rates for experienced welders, cost of materials and additional cost of fire wardens, quality paperwork and refinishing, lagging or repainting, welding can be more expensive than bonding especially if hot work is required.
Choosing the right method
If you prefer a cleaner appearance and ease of use, adhesive bonding can prove useful to your work. As a naval architect, welding is a preferred choice to achieve high levels of durability and strength for marine vehicles.
Advantages of Adhesive Bonding
From speed to cost to materials and overall aesthetic quality, still bonding has many advantages. Other areas of note include:
- Labour costs are reduced, requiring less training and expertise.
- Different materials can be used, allowing for metals to be easily isolated from corrosion.
- Bonds can easily be reworked, repaired, or disassembled.
- Aesthetics are improved, such as lack of discolouration and distortion.
- Thermal bonding is cost-effective in terms of energy use.
- Materials can easily be applied at room temperature, improving the comfort of workers.
Advantages of Adhesive Bonding
When compared to welding, marine bonded fasteners such as studs or stand-offs and cable mounts used with adhesive bonding have many advantages.
- It can be sealed and bonded within one operation.
- Bonding doesn’t distort or discolour metals and can be created at a low temperature.
- Can provide electrical and thermal insulation and protection from corrosion.
- Simplifies the design of the structure and saves weight.
- Bonding as a method can join irregularly shaped surfaces without disrupting dimensions.
- Stress is reduced on concentration points.
- Provides vibration and sound dampening.
Mechanical Properties of Bonding and Welding Materials
In the naval sector, bonding and welding processes require careful consideration of materials and mechanical properties. Each process must use a specific set of materials to guarantee long-term mechanical performance.
Using industry-approved materials ultimately helps to prevent corrosion, speed up the fusing process, enhance resistance to high temperatures, and result in a smoother, long-lasting finish.
Tensile strength
Tensile strength is the maximum stress a vessel can handle before breaking. When considering welding or adhesive joints, tensile strength plays a part in whether or not materials fuse.
During the steel welding process, the tensile strength must match the base material. Bonding materials may need a lower tensile strength due to the natural properties of adhesive material.
Stainless steel and galvanic corrosion
Stainless steel is chosen for joint strength and durability, suitable for both bonding and welding techniques. Bonding materials such as carbon steel and stainless steel can cause galvanic corrosion, so it’s important to consider the electrochemical properties of these metals and how they can affect your marine project.
While welding, heat can weaken the corrosive resistance of stainless steel, so specialised adhesives can prevent this problem.
Laser welding and dissimilar materials
For fusing together dissimilar materials without issues, laser welding is a popular technique for precise heat input and minimal distortion. Welding metals with unique melting points and thermal conductivities can be difficult, so this method trumps traditional welding.
Bonding dissimilar materials using adhesives can offer a versatile solution as it doesn’t depend on melting points for success. Whether naval architects use this method will depend on the end goal.
Resistance to corrosion
As 316 stainless steel is proven for its corrosion resistance, it is a popular choice for welding and adhesive joints.
With adhesive bonding, you need to be using the right materials for resistance to chemicals, moisture, and temperature. Welding requires post-welding treatments or protective coatings for resistance.
Flexible adhesives and joint strength
Designed to accommodate vibrations and movements, flexible adhesives are suitable for joints that experience thermal expansion or stress. While there is lower tensile strength compared to rigid adhesives, they can maintain structure under challenging environments.
Industrial applications
Bonding and welding have many uses for joint strength in industrial sectors. Welding is a heavy-duty application commonly used in construction, structural fabrication, and shipbuilding, whereas adhesive bonding is applied in electronics, aerospace, and electronics.
Temperature resistance
Welded joints are chosen for high-temperature resistance, such as extreme heat. As for adhesives, they need to match the operating conditions of the application. Often thermal protection is placed over the bonded parts to protect them from elevated temperatures.
Advantages of Metal Bonding
Metals can be quickly bonded instead of welded, and this can apply to manufacturing in the marine industry and sector. In contrast to more traditional joining technologies, bonding is a diverse alternative that is efficient, anti-corrosive, and well-suited to a wide range of different applications.
Efficient
Metal bonding is a faster application process compared to connecting screws and welding. Bonding adhesives are suitable for joints, overlaps, and sealing seams. There’s no need for an extra sealing step.
Aesthetic benefits
The bonding effects are invisible in a vehicle’s interior as MS polymer adhesives can work well with any material. Easy to paint over, the adhesive provides a smooth surface compared to using nuts and bolts.
Stress distribution
In comparison to other joining techniques, the tension of metal is distributed evenly during the welding process, creating a more durable bond.
Anti-corrosive
When two different metals come into contact, contact corrosion occurs. Metal bonding can prevent this. As an elastic adhesive, the metal protects itself against corrosion by creating a non-electrical conductive barrier.
What To Consider With Bonding Materials?
Bonding materials can be complex, so it’s essential to understand the materials used, and how to care for them after use. Here are some key questions to consider:
What materials need to be bonded? Are these materials external or internal? Are you looking to achieve a permanent bond, and is the surface rough or smooth? What will be the operating temperatures during service life?
Type of material
Depending on the type of metal being bonded, pre-treatment can be necessary to ensure the bond stays intact. For example, raw aluminium will require light abrasion and solvent wiping, but some adhesives need very little surface preparation.
Cleaning and pre-treatment
To obtain a more durable bond, surface abrasion or pre-treatment with an activator or cleaning agent is needed. A primer may be needed for stronger treatments. In most cases, an equal mixture of water and isopropyl alcohol can dissolve light grease, dust, and dirt.
What Are The Different Types of Welding?
The most common welding types include stick welding, MIG, TIG, and arc welding. Other methods include explosive welding, plasma arc welding, laser welding, and submerged arc welding.
Each welding method can be used for different purposes, such as bonding steel with special equipment. Understanding these methods can give you a better idea of how to plan your naval project, so what welding options can you consider?
Arc welding
Arc welding involves two materials welded together using electricity and can be protected by shielding gas, vapour, or slag. This method is useful with consumable rods, an electrode made of metal that melts while welded, and helpful tools for manufacturing steel products.
Arc welding is useful for construction, shipbuilding, and the mechanical industry. Plain carbon alloy, duplex steel, stainless steel, hard surfacing, and surfacing often use this welding type.
Stick welding
Also known as shielded metal arc welding, stick welding requires a stick welder, a ground clamp, a choice of electrode, and slag-removing tools to help prevent contamination.
This type of welding is less expensive, has portable equipment, is durable, and can be done outdoors. Likewise, it is commonly used in infrastructures such as roads, buildings, bridges, manufacturing, and steel fabrication. Apply this welding method to mining, aerospace, marine, shipbuilding, or nuclear fields.
TIG welding
Used commonly for sheet metals, TIG stands for Tungsten Inert Gas and benefits aviation, aerospace, and automotive as it decreases the risk of corrosion. TIG involves a more manual process, such as incorporating a welding torch, a welding power supply with a constant current, a gas for shielding, an electrode of choice, a grinder, and in some cases, filler metals.
If you aim for a safe and secure construction method, TIG welding helped the Internal Space Station project. TIG welding also assists in simple repairs, furnishings, and metal sculptures! Its strength can also repel water pressure!
MIG welding
Standing for Metal Inert Gas, MIG welding is known as the hot glue gun of welding. The method can be tricky when fusing materials, but it can often speed up the production time.
MIG welding requires a welding gun, a wire feed unit, a power supply, a consumable welding electrode wire, and a protective shield. In comparison to TIG welding, this method is less expensive. Materials used include stainless steel, aluminium, heavy-duty structural plates, and 26-gauge sheet metal, primarily used for boats, agricultural equipment, and mining equipment.
What are dissimilar materials?
When two metals have unique chemical compositions yet are welded together, these are dissimilar metals. This not only affects the welding ability but also the mechanical properties of these joints. Welding steel to copper is a classic example.
Metals Used for Navy Vehicle Manufacturing
- Magnesium. As a defence metal, it is one of the lightest materials used for structures such as military aircraft, spacecraft, or high-mobility vehicles.
- Titanium alloy. With superior heat resistance, titanium can’t be fractured easily, can handle lower temperatures, and is often used for aircraft structures, missiles and rockets.
- Rhenium. This metal is predominantly used to produce aero-engine blades and high-temperature components, such as for aerospace.
- Tungsten. Used to manufacture hard alloy and molten metals, tungsten is used for the aerospace and defence industries.
- Uranium. Uranium is a military metal used for nuclear reactions, weapons or plutonium for nuclear fuel.
- Molybdenum. Mainly used to manufacture hard alloy, molybdenum is used to manufacture weapons or materials used to build warships, satellites, and rockets. Materials include vanadium, tungsten, and chromium alloys.
Make Use of Military Fastener Supplies With Applied Fasteners and Tooling
At Applied Fasteners and Tooling, we supply high-end marine bonded fasteners that are purposely designed for the assembly and maintenance of naval defence ships. With markets extending from space to military and defence, there’s a tool to match any marine environment you’re working in.
Whether you’re looking for Click Bond Fasteners, Grip Lock Ties, Ball Lok Pins and Streamers, contact us today to experience a range of services to support your upcoming Navy project.