Why Countersink Cages Are a Critical Tool in Aerospace Manufacturing
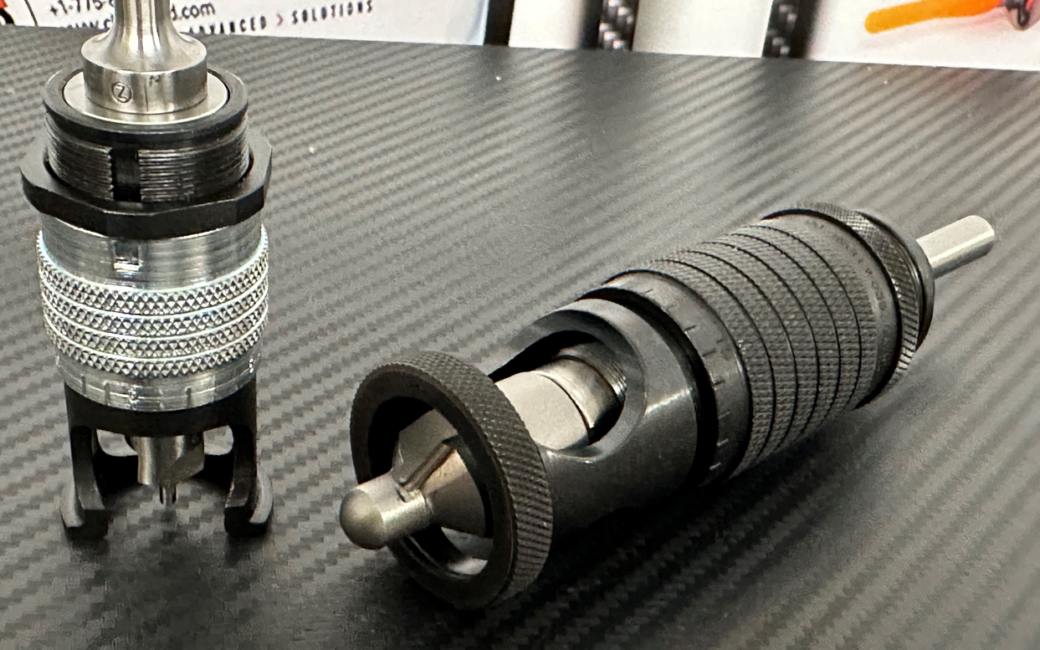
- May 09th, 2025
- Categories: Uncategorised
If you work in aerospace manufacturing, you’ll already know it is a highly regulated industry that relies on precision when it comes to fasteners and tooling. In these environments, even the smallest details will make a huge difference.
From the aerodynamic shape of a fuselage to the placement of each fastener, every piece of an aircraft must meet exacting standards. The countersink cage is designed to install flush fasteners on the surface of the aircraft’s structure, which is critical to aerospace manufacturing. It improves structural integrity, aerodynamic efficiency, and overall quality, making it indispensable across both commercial and defence aviation projects.
This article will explore the evolution of countersink cages, why they matter in aircraft production, how they’re used, and the latest innovations shaping the future of this tool.
Countersink Cages: History and Overview
The development of metal aircraft structures in the 20th century required precise countersinking. Early aircraft assembly was a more manual process, so the depth consistency for fastener seating was a challenge.
The invention of the microstop countersink cage unit in the 1930s transformed the process. Engineers could mechanically limit the depth of a countersink, creating uniform fastener fitment across hundreds or thousands of holes.
Today, units are much sturdier and more automated (and a lot more accurate) with better-bearing technology to achieve a higher RPM. A wing might be assembled on a large Gem-Cor machine, a jig where the wing is set. Pre-programmed robot drills countersink the hole in one operation using a combo drill/countersink.
So, how does it work? Two pieces of material need to be fastened in a way that doesn’t fly apart in a 90-degree turn; this means precision hole preparation is critical before a fastener is inserted. This is called countersinking.
Countersink cages are made with materials and coatings that handle the demands of cutting through composite materials such as titanium and other aerospace-grade alloys. A threaded-shank countersink is screwed into the unit with a handheld drill motor, allowing mechanics to adjust the depth of the countersink in 0.001” increments.
Why Do Countersink Cages Matter in Aircraft Manufacturing?
Countersink cages support aircraft safety, performance, and lifecycle for many reasons. Let’s take a look at why.
They Create Flush Surfaces
Raised or improperly seated fasteners can increase drag, so countersink cages make sure that every fastener sits perfectly flush or slightly recessed beneath the surface of the skin. The cages also maximise the level of airflow across the aircraft.
Flush fasteners also stop wear and tear, snags during handling or maintenance and contribute to a clean and professional finish.
They Increase Structural Integrity
Properly installed fasteners support load-bearing and stress distribution, and an aircraft needs to be reliable under great amounts of pressure in flight. A misaligned or shallow countersink can weaken structural joints or lead to stress fractures over time.
For example, commercial aircraft are routinely maintained to reduce the possibility of these failures. Using a countersink cage means each hole is prepared precisely to hold the fastener.
They Improve Aerodynamic Efficiency
Small surface disruptions can have large impacts on aerospace. Flush fasteners reduce surface turbulence, which in turn minimises drag and helps with fuel efficiency.
For high-performance aircraft (such as military planes), shaving off even minor inefficiencies can save operating expenses.
If you would like to learn more about how aircraft countersinking, have a read of: what are countersinks and why are they essential?
Types of Countersink Cages
There are several types of countersink cages, each suited to different stages of production or repair, depending on the scale and material involved.
Manual Countersink Cages
These are the most traditional and flexible types, supporting operator control in tight or awkward spaces.
Mostly used in maintenance, rework, and low-volume tasks where automation isn’t practical, manual depth adjustment is ideal for repairs and one-off modifications.
Automated Countersink Cages
Used in high-volume production, automated cages are integrated into CNC systems or robotic drilling units.
With precision and repeatability, these systems can be pre-programmed to perform countersinking operations on thousands of holes with identical results.
Diamond Countersink Cages
When dealing with materials like carbon fibre composites or titanium, traditional steel tools don’t last or do the job as they should!
Diamond-tipped or diamond-coated countersink cages are designed for high performance in demanding environments. They resist wear and produce results even when used for long periods.
What do you need to think about when performing countering applications?
Countersink cages help with depth control, but the conical recess must match the fastener type being used, such as a rivet or locknut. In aerospace, even a fraction of a millimetre off-spec can result in part rejection!
The cage fits over the drill bit and uses a depth stop to control how far the cutter enters the material. It is performed after drilling and before fastener installation.
Set everything up correctly. Operators set the depth using calibration tools or micrometres, then lock the setting in place. During operation, the cage provides a stable guide for a clean, chatter-free cut.
For automated systems, software control depth is based on CAD or CAM models, adjusting in real-time to compensate for tool wear or surface irregularities.
Are you interested in other fasteners, tooling, or consumables? AFT supplies Dotco Tooling, Hand Tools, Rivet Tooling, Specialty Fasteners, and Cable Tie Mounts.
How Do You Choose Countersink Tools?
Materials, coatings, geometry, and technique will influence the type of countersink tooling that you use for your project, but let’s look at this in more detail.
What is the tool’s life, and how durable is it? For example, tools with tungsten carbide or diamond coatings last longer, slashing downtime and maintenance expenses. For operations machining high-temperature alloys or composites, durability is essential.
Is the material compatible? Not all countersink cages are suitable for all materials. Aluminium needs a geometry that is different from carbon composites or titanium. Using an incompatible tool can lead to poor finishes, delamination, or even component failure.
What is the size of the countersink drill bit? Pick one that works for the bolts or screws you want to use. A drill bit that is too small isn’t big enough to fit a fastener.
Is the operator efficient enough for the task? Lightweight, ergonomically designed cages cut the chances of operator fatigue and improve accuracy in manual tasks. In automated setups, fast-change adapters and quick calibration systems help reduce changeover times and increase productivity.
Zephyr Tool Group, for example, provides tools built to meet the demands of the commercial and military markets. What are some drill attachment options?
- ZT627/ZT628/ZT629 Series High Speed Drill Attachments. A flat offset angle drill that is designed to run at any speed up to 6,000 RPM in the tightest and most demanding applications. It is well-suited for metallic, graphite, and composite materials used in the airframe industry today.
- ZT417 Angle Drills 90 Degrees Light Duty. These small, compact drills are designed for extra “tight” spots and are similar in construction to the larger models, except that, because of mechanical limitations, a ground steel spindle bearing is used instead of a radial thrust ball bearing.
- ZT246 Angle Drills 360 Degrees Standard Duty. This is a true “all angle” swivel heat-type tool for all standard duty drilling operations.
Let’s look at Zephyr’s microstop countersink cages.
- ZT680:SW Swivel Shaft. Machined for continuous operation at speeds up to 6,000 RPM without overheating. Countersink with up to a 5-degree off angle between the spindle and the cutter axis.
- ZT691/ZT692 High Speed Precision Microstop Cage. These offer a .0005” depth adjustment and are available with a full range of footpieces.
- ZT355, ZT357, ZT358 Series Long Travel Microstop Countersink Cages. The positive non-slip lock ring adjusts without tools and has a spring-loaded retractable type shaft.
- ZT663 Series High Speed Microstop. Has been precision machined and designed for continuous operation at speeds up to 10.000 rpm without overheating.
Manual vs Automated Countersink Cages: Which is Best?
Manual Tools:
- Pros: High flexibility, ideal for repairs, and a low initial cost.
- Cons: More reliant on operator skill and inconsistent results in high-volume tasks.
Automated Systems:
- Pros: Precision, speed, and consistency across large batches.
- Cons: A higher initial investment, more complex setup and programming.
How do you know what the right tool for your aerospace project is? It depends on your production needs. Many manufacturers use a combination of both, leveraging manual cages for rework and automation for primary production.
For a detailed guide, read E-drill system vs. hand drilling in the aerospace industry.
Order Aerospace Countersinks at AFT Today
Countersink cages are not just another tool in a technician’s kit. From assembly lines to the environments of aircraft maintenance, these tools mean that all fasteners can work quietly, efficiently, and flush. Choosing the right type of cage for your needs (whether manual, automated, or diamond-tipped) impacts both product performance and production.
The good thing is, Applied Fasteners and Tooling can point you in the right direction. Emerging as a leader in the fastening system supply chain, we work closely with only the most innovative fastener-related technologies and companies that push the boundaries of what is possible.
Registered and AS9120 quality certified in 2014, we were founded to supply the aerospace and defence industries with specialised fastening products and technical support.
If you are on the lookout for Hi Lok Fasteners, Marine Bonded Fasteners, Spacecraft Fasteners, Motorsport Fasteners, or EMI RFI Shielding, AFT is a one-stop-shop for exceptional quality and delivery for fastening and tooling needs.
Contact us to shop in stock today and to get a quote. We supply a number of reputable brands to a range of markets and provide services such as application engineering support, product testing, and more.