Best Practices for Installing Cable Tie Mounts in Aircraft
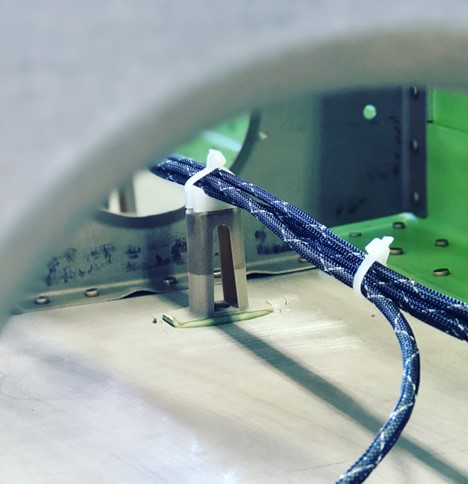
- May 16th, 2025
- Categories: Uncategorised
Every component matters in the aviation industry, and careful cable management solidifies the safety, performance, and longevity of an aircraft. Aviation cable tie mounts help to organise cables, improve signal transmission, and meet strict aviation standards, but what are the best practices when installing them?
In this article, we will discuss the best ways to install them in aircrafts, the types of cable tie mounts you can purchase, how to select suitable mounts for specific applications, and how to choose the best option for your aerospace project.
Let’s go into some brief history. Cable ties were invented and patented in 1958 by Thomas & Betts in the U.S., although they were first introduced as Ty-Rap for aviation uses. Originally made from stainless steel, cable ties transitioned into nylon and plastic in the 1970s.
Although stainless steel varieties are still manufactured today, plastic and nylon are popular (and come in many bright colours!). Here’s an overview of how to install cable tie mounts!
Use aircraft-approved materials.
- Only adhesives, mounts, and cable ties that are FAA/EASA-approved for aerospace use should be used.
- Components need to meet flammability, smoke, and toxicity requirements under FAR 25.853, for example.
- Materials must always be temperature-resistant, as low as -55°C and higher than 125°C, to resist fuels, oils, and hydraulic fluids.
Plan surface preparation.
- Use isopropyl alcohol (IPA) or aviation-approved cleaners to remove dirt, oils, or debris from the surface.
- Apply appropriate preparation for the substrate you are bonding to and solvent wipe again. Wait for the surface to dry completely before any application for stronger adhesive bonding.
- Avoid contaminants, such as touching the adhesive side with your fingers, as this reduces bond strength.
Consider a replacement strategy.
- Follow aircraft drawings or MRO guidance. Always refer to OEM instructions or aircraft maintenance manuals.
- Depending on the wire routing and bundle weight, place supports every 12” to 18”.
- Avoid moving parts and heat zones, keeping mounts clear of rudder systems, control cables, or high-temperature zones like engines or APU exhaust paths.
Think about the mounts you’re using.
- Only adhesive mounts can be used in low-vibration, low-load areas as temporary support. Allow the curing time (24 to 72 hours) before stressing the adhesive. Use verified bonded fasteners, screw-mount, or rivet mounts where weight, high vibration, or long-term support is required. Make use of torque screws to prevent damage or loosening and thread-locking compounds as needed.
With installation:
- Use the correct tension, as overtightening damages wires, and under-tightening allows movement and wear.
- Use a tensioning tool for consistency and to avoid over-compression.
- Identification cables must be readable; never obstruct the part number or data code labels with ties.
- Avoid sharp edges by routing ties so they don’t contact sharp metal or composite edges.
For inspection and quality control:
- Check adhesive bonding after 24 hours, especially before the final installation of cables.
- Ensure that adhesive mounts hold a light pull force (as per spec).
- Make sure that there is no lifting, peeling, or bubbles under the adhesive pad.
What environment will the aircraft be subjected to?
- The temperature must be correct during the installation process. Adhesives bond best between 15°C to 30°C and avoid installing below freezing.
- Mechanical fasteners are used in high-vibration areas such as near engines, landing gear, or APU compartments.
Document installation for traceability.
- Log every modification, such as the change to wiring or mount installation, in accordance with aircraft records.
- Use lot-tracked materials, especially for permanent installations. This ensures traceability in case of recalls or maintenance checks.
Make sure that cable tie mounts are easy to access during maintenance checks.
- Plan for serviceability and avoid blocking access to frequently serviced components. Route cables and mounts with future access in mind.
- Avoid over-bundling. Use service loops to prevent stress on connectors or wire terminations.
Some issues with cable tie mounts include weakening adhesives, cracks in the mount material, or broken cable ties. Maintenance and repairs can prevent these problems from affecting the aircraft’s performance. Applied Fasteners and Tooling offers a number of services, from product testing to repair and maintenance support.
Understanding Cable Tie Mount Types
Why do cable tie mounts matter? Also called wire ties or zip ties, cable ties bundle and secure aircraft cables and electrical wires. Aircraft are confined spaces, so being able to route these cables reduces wear, keeps pathways maintained and clear, and cuts the risk of electrical faults.
Vibration dampening from engines, turbulence, and manoeuvres in flight can cause cable movement and chafing, so cables with vibration-dampening properties mitigate the impact of these vibrations while ensuring the cables remain fastened. Cable mounts are also designed to be fire-resistant and self-extinguishing, critical to the overall fire safety of the aircraft.
Cable tie mounts come in various types, each with features designed to suit different environments and requirements. Let’s break down the main types of cable tie mounts used in aircraft:
Adhesive Cable Tie Mounts
Adhesive cable tie mounts are a popular option for aircraft because they can be quickly installed without the need for drilling or other mechanical fastening methods.
- Easy Use: They have an adhesive surface that allows them to be easily attached to different surfaces inside the aircraft without the need for drilling or extra fasteners. Installation is a lot quicker!
- Durability: Aircraft are subject to high vibrations, fluctuating temperatures, and other harsh conditions, so these mounts are made from high-strength materials that can withstand these extreme environments. The adhesives used are typically designed to endure these conditions without losing their bond.
- Compliance: Adhesive cable tie mounts used in aircraft are often made to meet aviation standards and regulations, such as those set by the FAA (Federal Aviation Administration) or EASA (European Union Aviation Safety Agency).
- Design: The mounts may have various shapes (such as square or round) and are available in different sizes depending on the cable’s thickness and application.
What are some of their applications? In avionics, adhesive cable tie mounts securely fasten wires, sensors, and other electrical components. They also secure cables in relation to HVAC or other environmental systems.
Heavy-Duty Adhesive Mounts
What are some of the features of heavy-duty mounts? There are many reasons to consider them for your upcoming project.
- Stronger Adhesive: Heavy-duty adhesive mounts use stronger, industrial-grade adhesives that can hold heavier objects or endure more stress. This creates a longer bond that can resist peeling, lifting, or failure under load.
- High Load-Bearing Capacity: They are designed to hold heavier components in place, such as thick wiring harnesses, electrical devices, or other heavy parts.
- Vibration Resistance: Heavy-duty adhesive mounts are built to withstand vibrations in applications like aircraft, vehicles, or machinery.
- Temperature and Weather Resistance: These mounts often feature adhesives that can handle a wide range of temperatures (both hot and cold).
- Versatile Surface Attachment: They can be applied to a variety of surfaces, including metal, plastic, glass, or composite materials.
- Quick and Easy Installation: Since they do not require drilling or additional fasteners, heavy-duty adhesive mounts save time and reduce the need for specialised tools during installation. This reduces the risk of damaging the surfaces to which they are attached.
- Permanent or Removable Options: Some heavy-duty adhesive mounts are designed for permanent attachment, while others allow for removal without causing damage to the mounting surface. The choice depends on the application’s needs and whether components might need to be replaced or relocated in the future.
- Customisation: Heavy-duty adhesive mounts can come in a variety of sizes, shapes, and configurations. Whether it’s for securing large cables, routers, antennas, or other heavy equipment, there are many options for engineering projects.
Screw-Mount Adhesives
Screw-mount adhesive cable tie mounts combine the benefits of both adhesive and screw-mount systems.
- Dual Attachment Method: Screw-mount adhesives offer a simple two-step attachment process. The adhesive provides an initial bond that holds the mount in place, and then screws (or bolts) provide additional security.
- Enhanced Load-Bearing Capacity: The adhesive bond holds the mount in place, and the screw or bolt helps it to securely fasten under stress or vibration.
- Vibration Resistance: The adhesive provides a strong bond to prevent slippage or loosening.
- Versatility: Screw-mount adhesives can be used on metal, plastic, wood, and composite materials, so they are compatible with aircraft.
- Easy Installation: The adhesive layer allows for easy attachment without the need for pre-drilling or complicated preparation. The adhesive sticks to the surface, and once in place, screws or bolts are used to secure the mount firmly. It saves time, and there’s no need for heavy tools.
- Permanent or Semi-Permanent Bonding: Do you need to replace or re-position a component? Some screw-mount adhesives provide a permanent bond, while others offer a removable option.
- Weather and Chemical Resistance: Screw-mount adhesives handle extreme temperatures, moisture, and exposure to chemicals.
How are they so different from standard cable ties? Standard options have a one-piece, self-locking fastener and are designed for single use. They have a tensile strength from 8 to 144kg.
What About GripLockTies?
- GripLockTies Releasable Rubber Lined Zip Ties solve the problems of damaged wires and cuts into structures and painted surfaces.
- Traditional cable ties can loosen when the pressure deforms the wire and cuts the wires or, worse, cuts through the paint and structure and causes damage.
- The rubber lining pads, wires and structure hold it stable under vibration and eliminates the damage of old slip ties, saving time, weight and money over P Clip style metal clamps.
- GripLockTies were developed for aerospace and motorsport with UV protection, higher heat rating, and a super strong positive latch. They can be repositioned during construction and then clipped flush.
- Available in standard UV Protected Black Dupont Nylon with Red or Blue or Orange Rubber-Lining.
Selecting the Suitable Cable Tie Mount for Aircraft
Selecting the right cable tie mount for an aircraft involves evaluating several factors to ensure durability, functionality, and safety. Different mounts serve distinct purposes depending on the application and environment.
Is a Cable Tie Right For Your Aircraft Project?
From commercial aircraft to military defence planes, there are many things you need to consider:
What is the surface material? An adhesive mount may not work with oily or textured surfaces.
What are the environmental conditions at flight? Consider the temperature range, humidity levels, and exposure to chemicals or UV radiation.
What is the load capacity? The mount’s load capacity should match the weight and quantity of cables it will support. Overloading mounts can result in failure or degradation.
What is the vibration resistance? Aircraft are subject to significant vibration, so investing in a cable mount with vibration resistance stops cable tie mounts from loosening.
If you are weighing up the pros and cons, read this blog to make an informed choice: cable tie vs GripLockTies: which is right for you?
What are some useful cable tie mount applications?
Cockpit and avionics are where electronics and critical communication systems are located. Cable tie mounts with high-temperature resistance and low outgassing properties are important.
The wings, or fuselage, experience vibration and dynamic forces. Heavy-duty adhesive or screw-mount adhesive cable tie mounts are recommended to put a stop to mount failure.
The cargo area isn’t subjected to the same temperature extremes or vibrations, so lighter adhesive mounts are suitable. However, always verify the mount’s adhesive strength and ability to handle the weight of the cables.
If you would like to learn more, have a read about exploring the uses of cable tie mounts! AFT offers a personalised interaction and value-added service in technical support through the product life cycle, working with design, procurement, production, quality, maintenance and repair.
Cable Tie Mounts at Applied Fasteners and Tooling
AFT is proud to provide specialist products and technical support across a wide range of fastening technologies. We supply a variety of cable tie mounts, including composite cable ties, small cable ties, and Turks Head cable tie mounts.
For more information or to request a quote on the cable ties you need, get in touch with our team. We also supply Hi Lok Tooling, Specialty Fasteners, Eddie Bolt Tools, Countersink Tooling, Hand Tools, AN, MS, and NAS Hardware, and a range of Drilling Equipment.
Contact us today to learn more about the markets we work with, brands we supply and to shop in stock.
By picking the right mount type, adhering to industry standards, and regularly maintaining the system, aircraft operators can improve their fleets’ safety, performance, and durability.