Click Bond Fasteners: Revolutionising Aerospace
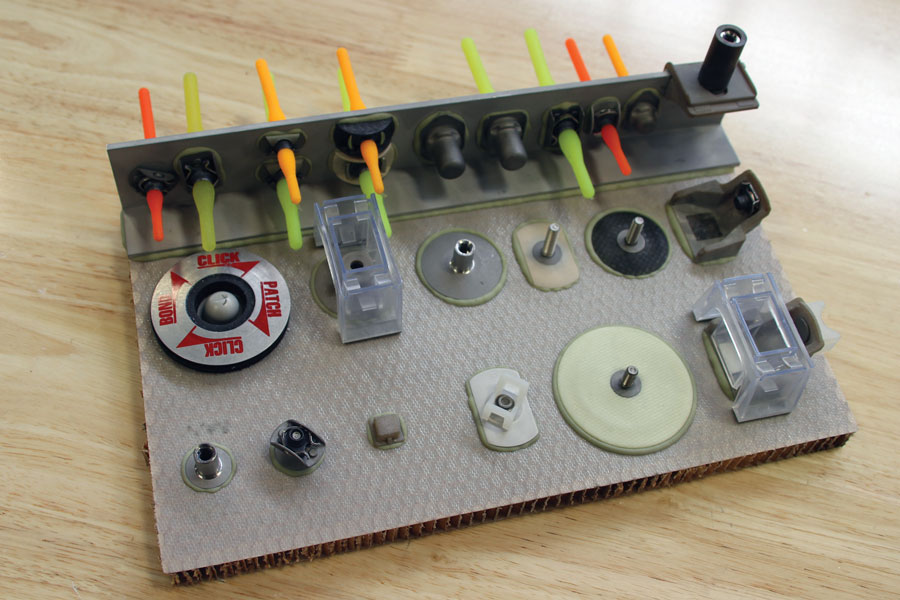
- February 16th, 2024
- Categories: Uncategorised
First developed in the US more than 35 years ago, The Click Bond fastening system has revolutionised the aerospace industry and opened doors to various applications, tasks, and methods.
Click Bond offers unmatched performance and precision, and its state-of-the-art tools have proved critical for land, sea, and air applications. These innovative adhesive bonds benefit areas of the aerospace industry, specifically commercial and military aircraft. With these fasteners, you can preserve structural integrity, save weight, and simplify installation, rework, repair time, and overall costs.
This article will explore the advantages of Click Bond mechanical fastening methods and how they support aircraft in all environmental conditions.
Click Bond Fasteners – Background and History
In 1987, inventor and ATP-rated aircraft pilot Charles Hutter and his wife Collie founded Click Bond Incorporated as a subsidiary of Physical Systems. Click Bond products were first manufactured in Carson City, Nevada, and Hutter remains involved in product design, development, and patenting.
Since their foundation, they have proudly supported global leaders in the manufacturing and design of high-performance systems, including their signature Click Bond fasteners. These fasteners result in lighter, faster, stronger, safer, higher value, and longer living products.
Click Bond also develops all of its products in line with AS9100 requirements, ensuring all fastening and tooling suppliers always deliver top-quality products and materials.
Advantages of Click Bond Fasteners
Source: LoMas Screws – Click Bond
Click Bond Fasteners are an adhesive bonding solution designed to simplify installation and maintenance, but with so many other fasteners on the market, why are they worth the investment? Let’s explore the many reasons to use them in high-volume applications.
1. No holes are required
With adhesive bonding studs, engineers can use a clamp attachment with wire bundles and tubing where a bolt and nut combination is complex. Click Bond Fasteners are also well-suited for securing junction boxes, enclosures, or other modular equipment.
As Click Bond Studs are available in many metal and composite materials, you can expect installation fixtures with accurate positions. The fastener will be held under positive pressure while the adhesive cures, optimising bond strength.
2. Weight savings
Do you need weight reduction in non-structural applications, such as system routing or interior component installations? The LoMas Screw offers up to 50% in weight savings, a revolutionary lightweight threaded fastener design!
This LoMas Screw is a hollow shank with a low-mass construction, utilising materials with excellent strength-to-weight properties.
3. Drilling isn’t required
Adhesive bonded mounts eliminate the need for drilling. With an advanced and flexible design, Click Bond Fasteners support routing systems and protective blankets in new construction and retrofit applications! There is no need to stress structural integrity, cost, and restrictions.
These adhesive bonded mounts are available in baseplates and bodies manufactured from metallic and non-metallic materials. Likewise, the thermoplastic saddles of cable tie mounts contain fixed and swivel options with a latching hasp.
4. Minimise drill plates and drilled holes
Click Bond provides adhesive bonded rivet less nut plates, so drilling attachment rivet holes is unnecessary, unlike traditional riveted nut plates. With these nut plates, you can preserve structural integrity, save weight, and reduce installation and repair costs.
Click Bond nut plates are FAA TSO approved and meet the performance requirements of NASM25027, including applications requiring 50-cycle reusability with titanium or stainless steel bolts.
5. Economical solution for oversized holes
If you need to add structural fatigue life, Click bond ACRES Sleeves are excellent for engineered repairs. Thin walls and deep-drawn stainless steel sleeves are designed to prevent oversized hole conditions from corrosion, manufacturing error, and in-service fatigue.
6. Preserve structural integrity
Does your project require the separation between systems, structure, and components? Adhesive bonded standoffs are suitable, with an extensive range in multiple lengths, thread sizes, and locking or non-locking threads.
Installation for constrained footprint applications is easier, cutting back disposable waste and eliminating the fixture removal process.
7. Repair leaking fasteners and light damage
Looking for an approved standard repair for commercial or military aircraft? Click Patches are adhesive-bonded patches that provide an inexpensive, rapid repair of leaking fasteners in skin punctures, wet-wing aircraft, and other light damage.
These patches can be applied directly over a running leak without refuelling. Available in composite and metallic materials, these patches are compatible with many substrates and reduce aircraft downtime.
If you’re seeking supplies to support the safety of critical applications, Applied Fasteners and Tooling provide Click Bond Fasteners, GripLockTies, Aerospace Tooling, Cherry Tooling, Eddie Bolt Tooling Spares, and more.
Common Types of Adhesives Used in the Aerospace Industry
Source: Adhesives – Click Bond
High-strength adhesives, such as those used to create Click Bond fasteners, are critical to the aerospace industry. This is because there is a constant demand for strength and weight reduction, and various types of adhesives meet this necessity.
During the design and manufacturing phase, Click Bond’s fasteners are created in line with multiple OEM specifications. Each of these tools is designed to minimise component ratio and mix consistency, which helps them to better facilitate adhesive application.
Common adhesives used in the aerospace industry include:
Anaerobic adhesives
These adhesive types are used for retaining, thread locking, thread sealing, and form-in-place gasketing. Often used in the engine compartment, these applications prevent vibration loosening throughout the aircraft.
Structural acrylics
Used for diverse applications such as bonding magnets into electric motors and attaching harness clips, Permabond structural acrylics are critical for adhesive bonding.
Cyanoacrylates
Used to bond various items permanently, cyanoacrylates instantly hold parts as they are being bonded with slower-curing adhesives. As a quick fix for damaged interior trim, this takes seconds to cure.
Epoxies
Permabond ET5428 and ET5429 bond carbon fibre and other substrates. Honeycomb edge fillers are lightweight for bonding composite materials, often epoxy-based with low density, keeping aircraft as light as possible.
Want to learn more about aerospace drilling for fasteners? Check out the comprehensive guide to E-Drill 2.0 System vs Hand Drilling in the aerospace industry!
Composite Materials in Aerospace
Click Bond studs and standoffs are available in many composite materials for automotive, industrial, and aerospace applications.
Compared to dissimilar materials, composite materials are fibre-reinforced polymer composites, such as glass, carbon fibre, and aramid fibre combined with epoxy. They are created by combining two different materials on a macroscopic scale.
According to this Composites Aerospace Applications whitepaper, commercial and military aircraft require the development of improved structural materials, and composite materials play a role in current and future aerospace components.
With exceptional stiffness-to-density ratios, corrosion resistance, greater fatigue limits and increasing lifespan, composite materials have superior physical properties and often replace metals.
Aircraft Construction – Importance of Composites
Why are composite materials so important during aircraft manufacturing processes? With many design capabilities, mechanical engineers use them for many reasons.
- Using composite materials results in more options for the design geometry of aircraft structures. Composites are well suited for compound curves and organic shapes such as engine cowlings, wing tips, and wheel fairings.
- Composite materials benefit aerospace with toughness, temperature capability, density, conductivity, fatigue life, cost, and chemical compatibility.
- Aircraft can fly faster, higher, and farther distances while carrying higher payloads.
- With fibre reinforcement, composites for aircraft provide stiffness and strength in the direction in which the fibres are aligned. Having different chemical compositions, these fibres generate different physical and mechanical properties at the macroscopic level.
- Composite materials are versatile since mechanical and physical properties can be fine-tuned by adjusting the composition of a specific material.
What About Traditional Fastening Methods?
Traditional mechanical fasteners will always play a role in aerospace applications. Here is a quick overview of their uses and limitations compared to composite materials.
Riveting. By joining two or more materials with a metal pin through aligned holes in the materials, the end is deformed to form a second head. This creates a permanent connection. This method is used in aerospace for joining aluminium for strength. Riveting can be time-consuming and adds weight to the structure with the stress concentration.
Bolting. This involves using bolts, washers, and nuts to join two or more components. As threaded fasteners create a semi-permanent connection, bolting is used for assembling components that need frequent or periodic replacements. Regarding their limitations, bolts can loosen over time due to vibrations or thermal cycling.
Welding. Welding techniques such as Tungsten Inert Gas and Gas Metal Arc welding can join aerospace structures for high strength and durable connections by melting and fusing materials to form a strong joint. It is important to consider how heat-affected zones alter material properties. If unsure, speak to a fasteners and tooling specialist for advice on improving overall performance.
Applied Fasteners and Tooling – Choose Spacecraft Fasteners
Seeking innovative solutions for industrial, commercial, and defence applications? At Applied Fasteners and Tooling, we supply and support a range of bonded fastening solutions from Click Bond. With a comprehensive range of Click Bond Fasteners and reliable technical support, AFT is a key supply chain provider.
We have everything you need for aerospace and specific engineering applications, including Cable Tie Mounts, Hi Lok fasteners, AN fasteners, MS fasteners, Grip Lock Ties, Avibank Ball Lock Pins, Click Bond Fasteners, Adhesives and Equipment and a range of handy tools for your upcoming project. We supply quality fasteners and assembly tooling consumables worldwide to the space, defence, industrial platforms, marine, transport, and aerospace industries.
Registered and AS9120 Qualified in 2014 by approved standards, we supply the aerospace and defence industries with specialised products and trustworthy technical support. All parts are supplied with certificates of conformance to customer requirements. You don’t need to stress about your design and manufacturing operations with us.
Our services cover application engineering support, product development and training, product testing, program management, and repair and maintenance support.
Contact us today to explore the boundaries of what is possible!