Cold Working Fasteners and Tooling – Supporting Aerospace and Defence Applications
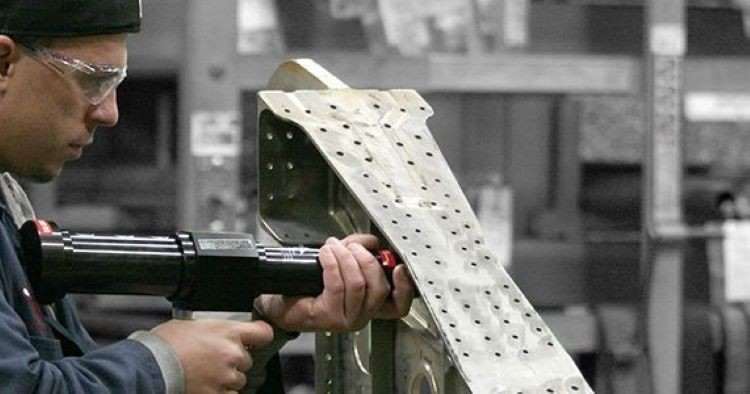
- February 20th, 2024
- Categories: Uncategorised
Aerospace and defence sectors require the best in manufacturing, and cold working fasteners and equipment are one of many applications that keep aircraft operational in the toughest conditions.
Eliminating or reducing crack growth around the hole, the primary function of cold working fastener holes is to strengthen metallic components. Producing this residual compressive stress zone acts as a barrier, reducing the stress intensity factor and localised stress ratio.
As well as being a fatigue life enhancer, these tools have many benefits, which is why complex industries like defence and aerospace rely on cold working technology for various applications.
This article is an informational resource on cold working fasteners and tooling, including why they are necessary and practical examples of these applications within the aerospace and defence sector.
What is Cold Working?
Unlike hot forging, where the metal is heated, melted, and solidified, cold working causes the material to deform at room temperature and can improve tensile strength.
As the plastic deformation of metals below the recrystallisation temperature, cold working is generally preferred over traditional manufacturing (such as machining). This is primarily due to lower scrap rates, reduced raw material usage, and downstream processes.
Cold forming processes can include squeezing (such as forging, extrusion, cold rolling, heading, and thread rolling); bending (such as roll bending and angle bending); shearing (such as piercing, blanking, and cutting); and wire drawing, tube drawing, or embossing.
Cold forming can yield over two times more parts than the same machined part. Engineers should create and design economic components that keep costs minimal.
Dimensional Accuracy of Cold Forming
All manufacturing conditions impact the accuracy of a cold-formed part, and it is important to understand the impact it can have.
Factors that affect the dimensional accuracy of cold-forming are the machinery type, process, and condition, tooling accuracy, raw material quality, operator experience, in-process controls, and lubricant type, all of which play a critical role in the final result
Cold forming techniques
What are some of the best cold-forming practices?
- Always use practical tolerances on all dimensions; avoid sharp corners, undercuts, and chamfers;
- Use simplified geometry if possible; call out practical concentricity, flatness, and parallelism;
- Define functional finish requirements such as heat treating, consider the materials optimised for cold forming, and understand the mechanical properties specified by the desired design.
Cold-forming surface finish depends on tooling finish and wear. At AFT, our ColdWork Tooling and fasteners–such as the Mandrel Gauge–are critical to the finished part’s accuracy.
Benefits of Cold Working Fasteners
In the defence industry, there are many manufacturing processes – such as using higher temperatures – but what are the unique advantages of cold working techniques?
- Increased strength: By inducing plastic deformation without altering the chemical composition of materials, cold working makes fasteners more resistant to deformation and failure under loads.
- Improves hardness: Compared to untreated fasteners, cold working helps fasteners withstand wear and abrasion.
- Dimensional accuracy: Cold working can improve the surface finish of fasteners, supporting compatibility and fit with mating components.
- Fatigue resistance: Cold working improves the fatigue resistance of fasteners, ensuring they aren’t prone to failure from repeated loading and unloading cycles.
- Cost-effective: Compared to hot working processes, cold working requires less energy and resources and is excellent for producing high-strength fasteners.
- Reduces material degradation: Cold working is performed at or near room temperature, so there is minimal risk of oxidation or grain growth.
- Wide range of materials: As a versatile manufacturing technique, cold-working processes can be applied to steel, aluminium, titanium, alloys, and composite materials.
Residual Stresses in Fasteners
Residual stresses can remain in an object- such as a welded component- and exceeding this elastic limit may result in deformation. This impacts an object’s distortion, fracture, or fatigue. With this in mind, what are residual stressors and what causes them?
Causes of residual stresses in fasteners
Residual stress can occur in many circumstances, and it is important to identify them early.
- Thermal variations: Once an object is cooled from high temperatures, there is a difference in the cooling rate experienced by the object’s exterior and interior. These thermal contractions can cause non-uniform stressors. When the surface cools, the heated material at the centre is compressed, whereas the material in the middle is constrained by the outer material.
- Mechanical processing: Occurs when plastic deformation is non-uniform throughout the cross-section of an object under manufacturing processes; this can include drawing, bending, rolling, or extruding. During deformation, one part of the material is plastic and the other elastic.
- Phase transformations: A volume difference exists between the newly formed phase and the surrounding material during a material underlying phase transformation. Volume differences cause expansions or contractions of the materials, hence residual stress.
Want to learn more about different fastening and tooling techniques? Have a read of what is better for navy environments, bonding or welding on the Applied Fasteners and Tooling blog page!
Impact of residual stressors on fastener performance
Depending on the distribution, magnitude, and application, residual stressors in fasteners can positively and negatively impact performance.
Positive effects
- An increase in strength: Residual compressive stressors can boost the load-carrying capacity of fasteners. By counteracting tensile stresses that develop during under-applied loads or tightening, there is less likely to be corrosion cracking and better fatigue life.
- Improved joint integrity: Prevent fastener loosening or relaxation of the joint under cyclic loading conditions.
- Sealing applications: Promote better contact between mating surfaces and reduce fluid or gas leakage.
Negative effects
- Stress corrosion cracking: In corrosive environments – such as near seawater – residual tensile stresses can promote cracking and failure in fasteners.
- Hydrogen embrittlement: Fasteners can be more susceptible to mechanical damage when absorbing hydrogen – such as high-strength steels and alloys – leading to catastrophic failure.
- Relaxation: Due to temperature cycling, creep, and material relaxation, joint integrity can be compromised.
- Distortion: When fasteners or mating components distort or warp, this affects assemblies’ fit, function, and look.
Mitigating Residual Stress
What can be done to prevent residual stress? Mechanical engineers need to keep in mind these techniques.
Implement post-treatment processes
Stress-relief annealing. Using controlled heating and cooling processes–such as stress relief annealing– can re-distribute and reduce residual stresses, often more effective with high-strength steels and certain alloys.
Shot peening. Bombarding the component’s surface with small spherical particles at high velocity improves fatigue resistance.
Material selection
- Low-residual stress materials. Choosing certain aluminium alloys or maraging steels can stop the need for mitigation.
- Thermal stability. Select materials with good thermal stability.
Design optimisation
- Stress concentration reduction. Choose components designed with smooth transitions, fillets, and radii.
- Load distribution. Ensure loads are distributed evenly across structures or joints.
Controlled manufacturing processes.
- Controlled machining parameters. Cutting speed, feed rate, and tool geometry can stop residual stress due to turning, milling, and grinding.
- Precision control. Using precise manufacturing techniques can reduce the likelihood of process-induced distortions in the finished component.
Pre-treatment methods
- Cold working. Intentionally cold working, such as cold forging or cold expansion techniques, can enhance its resistance to corrosion cracking.
- Preloading. Apply preload to fasteners during installation, as this prevents the development of tensile residual stresses.
Split Sleeve Cold Expansion Technique
The Split Sleeve Cold Expansion Technique (SSCE) helps to prevent fatigue cracks and repairs the structure where damage has been done.
The Split Sleeve Cold Expansion technique increases fatigue life by 3:1 and can be applied to diverse aerospace and structural applications.
If you would like to learn more about cold expansion fastening and tooling, consider Cold expansion Systems !
Common Cold Forming Products
A wide variety of products can be manufactured using cold working, which is excellent for fit installation.
- Fasteners: Commonly used to form a wide range of fasteners such as sleeves, bushings, bolts, screws, nuts, rivets, and other threaded components, fasteners are essential to the aerospace and defence industries worldwide.
- Bearings: Ball bearings, stainless steel balls and roller bearings can be produced using cold-forming processes.
- Medical devices: Orthopaedic implants and surgical instruments are manufactured using cold-forming techniques for precision and high strength.
- Hydraulic and pneumatic components: Parts for valves, couplings, and fittings are cold-formed for hydraulic and pneumatic systems.
- Construction hardware: Hardware such as screws, nails, anchors, and brackets are made with cold-forming techniques.
- Energy industry components: Power generation and distribution equipment is manufactured with cold forming.
- Plumbing and HVAC components: Pipe fitting, couplings, and connectors can be made using cold forming.
Applied Fasteners and Tooling – Trustworthy Aircraft Tools
Aiming to prevent compressive stresses and cracks in holes with your next project? At Applied Fasteners and Tooling, we have everything you need for aerospace and industry-standard engineering applications, including Deburring Tools, Cable Tie Mounts, Clecos and Temporary Fasteners, Composilok and Visulok Tooling and a range of handy tools for fatigue life improvement.
We supply quality fasteners and assembly tooling consumables worldwide to the space, defence, industrial platforms, marine, transport, and aerospace industries.
Registered and AS9120 Qualified in 2014 by approved standards, we supply the aerospace and defence industries with specialised products and trustworthy technical support. All parts are supplied with certificates of conformance to customer requirements.
Meeting the Quality Assurance Procurement Requirements without fail, you don’t need to stress about your design and manufacturing operations with us.