Essential Factors to Consider When Choosing Aircraft Cable Routing
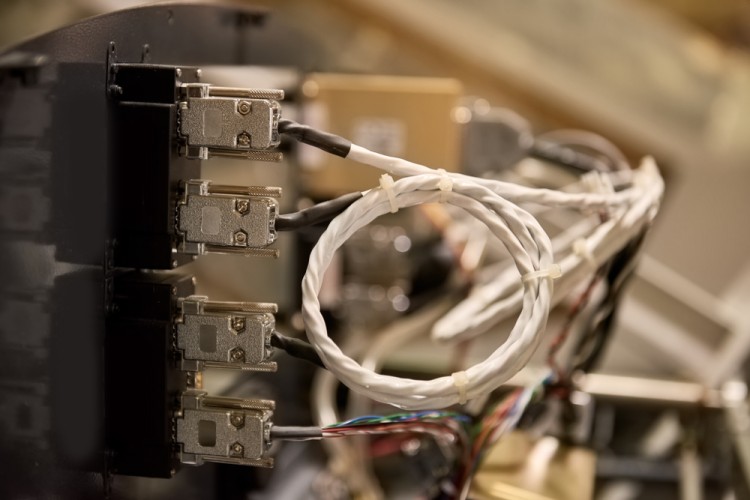
- February 03rd, 2025
- Categories: Uncategorised
As an engineer in the aviation field, it is critical to consider how you’re routing aircraft cables.
Electronic systems support the safety, reliability, and performance of aerospace vehicles. Aerospace-grade wiring specifically provides essential connectivity for instrumentation, power distribution, and communication.
Modern aerospace electronic systems require high-performance wire and cable for commercial airliners and sophisticated satellites. When configuring these systems, it’s important to think about the materials, design, and performance standards to meet the demands of extreme conditions.
This blog will be your guide to aircraft cable routing precautions when moving forward so that your project meets strict performance standards. After all, you don’t want lives to be at risk.
Aircraft Cable Routing: What to Consider?
Let’s look at some of the components of aircraft cable routing.
Components of Aircraft Cable
What are some of the common selection choices for aerospace wire and cable composition and construction?
Conductor material
- Aluminium is used in applications where weight reduction is a primary concern and in non-dynamic applications.
- Copper is used due to its high conductivity; aerospace copper wire is coated with silver, tin, or nickel.
Insulation material
- Cross-linked ethylene tetrafluoroethylene (XL-ETFE) supports higher heat resistance, improved durability, and thin-wall XL-ETFE, saving weight without compromising performance.
- Ethylene tetrafluoroethylene (ETFE) is known for its excellent chemical resistance and high-temperature performance.
- Fluorinated Ethylene Propylene (FEP) offers similar properties to ETFE but with improved flexibility for high-speed data cabling.
Shielding Type
- Braided Shielding protects against electromagnetic interference (EMI), radio frequency interference (RFI) and crosstalk, especially in differential data cabling.
- Aluminium Mylar Shielding offers a lightweight and effective tape-wrap shielding solution.
- Semi-conductive jacketing maintains a constant voltage gradient and reduces corona discharge.
- Microfilament Braided Shielding provides weight reduction, better flexibility and reduced windowing.
Temperature Rating
- Standard temperatures are suitable for normal operating conditions.
- High temperatures are designed to withstand elevated temperatures encountered in aerospace applications.
- Low-temperature is engineered for use in extreme cold or cryogenic environments.
Voltage Rating
- Low Voltage, which is typically used for signal and control applications.
- Medium Voltage is suitable for power distribution within aircraft systems.
- High Voltage is used for high-power applications such as electric motor propulsion systems.
Application Specific
- Communication Cables are designed for transmitting high-frequency RF and high-speed protocol (Ethernet) data within the aircraft.
- Power cables are used to distribute electrical power throughout the aircraft.
- Specialty Cables are tailored for specific functions or behaviours such as grounding, bonding, current return network, etc.
- Instrumentation Cables are employed by connecting sensors, gauges, and other devices.
Factors That Affect Cable Routing
What can affect aerospace cable routing?
Identifying the application and its requirements early in the design process to avoid over-designing cable assemblies that cost too much or under-designing them that fail to meet the system’s requirements.
Choose the best conductor materials for most assembly applications. For example, various copper alloys offer increased hardness, tensile strength, flexible endurance, and temperature resistance. Alloys are better suited to fine-gauge applications, such as AWG or smaller.
The flexibility of the cable. For example, high-tensile strength alloys allow for longer flex life. This higher flexibility (achieved by finer stranding) leads to a longer life span.
Choosing the correct conductor size, as it should be selected based on the necessary power load of the application. For example, ambient temperature always needs to be taken into consideration when selecting the conductor size of the cable.
Wire Harness Assembly
The electrical wire permitted for use in military aircraft is identified by MIL-W-22759/16. Although electrical wiring can be found at your local auto parts store, it does not stand up to military-grade cables (the insulating coatings give off toxic fumes in the event of a fire).
So, the most important consideration is that the wire must be made up of twisted wire strands instead of a single solid wire core. Stranded wire handles vibrations and is less likely to break.
What about techniques for effective installation? According to an article published in 1995 by the EEAA, the crimping tool has been used to secure the wire to a reliable connector at each end; these connections are made using insulated crimp terminals.
LUBBERING created the Roll Profi FLEXIPASS cable management tooling that helps prevent damage to cables, especially for harsh cable tray installation on sensitive data and power cables. It is the universal cable routing system for all kinds of cable trays.
Electromagnetic Interference
When it comes to safe cable management, they must be designed and installed so any electrical interference likely to be present in an aircraft will not result in hazardous effects on the plane or its systems.
The FAA has a guidance document on this regulation; engineers must look at the following sources of EMI:
- Electrical coupling or cross-talk between electrical cables
- Electrical noise generated from the equipment connected to bus bars
- Electrical coupling between aerial feeders and cables
- Static discharge or lightning currents
- Parasite eddy currents and voltages in the EWIS and grounding systems
- Electrical equipment operating out of spec or malfunctions generating EMI
What methods are commonly used in the aerospace industry to protect against EMI? Using EMI or electromagnetic pulse filter protection connectors or signals, route power wires through separate connectors.
If cable shielding isn’t protecting the signals, additional methods for protection need to be considered, such as increasing the separation distance or adding shielding to the cables. For more information, explore the critical role of EMI/RFI shielding for military defence.
Material Selection for Cable Routing
What are some things you need to think about when choosing a material?
It needs to be fire-proof and achieve flame retardancy. This can be with halogens added to the plastic or halogen-free flame retardant, or synergists, which are materials that provide a higher threshold of flame retardancy. A synergist consisting of halogen-free aluminium trihydrate and silane components is a great option, as aluminium trihydrate reacts with fire to form aluminium oxide and water, taking heat from the fire and forming a crust of burnt material that serves as a protective layer.
Use a protective jacket to resist lubricating oils, grease and cleaning agents. For example, special cables have sheaths made of polyvinyl chloride or polyurethane (PVC), which is the industry standard for most cables as they are easy to extrude and resistant to many oils and chemicals.
Where a plug connector meets a switch cabinet, the seal must be as hard-wearing as other materials in the installation. For example, fluorocarbon rubber (FCM) is resistant to weathering, ageing, chemicals, ozone, and handles extreme environmental conditions except below -20 degrees. For colder spaces, silicone is more suitable.
Choose stainless steel as it does not rust or have a coating that can break down; V4A is a resistant alloy that can handle hard abrasion, such as hard brushes used for cleaning.
Compliance with Industry Standards
What are the relevant regulations for aerospace-grade wire and cable? It is important to adhere to specific standards in aviation for stringent performance, safety, reliability, and quality requirements.
- SAE AS50881, which covers the selection and installation of wiring used in aerospace vehicles.
- NEMA-WC27500, which specifies requirements for aerospace and defence multi-conductor cables. This includes their construction, materials, performance, and testing criteria.
- SAE AS22759, which sets the performance requirements for high-temperature aerospace hook-up wires, such as insulation and jacketing materials.
- ASTM D3032 and SAE AS4373, which are key performance and test specifications that define standard testing methods for hook-up wire insulation and insulation electrical wire.
If you would like to learn more about cable routing, have a read of aircraft cable management systems, safety in flight! For more information on guidance material for the maintenance of aircraft electrical systems, read this AC 21–99 v2.1 report by the Civil Aviation Authority.
What about heavy-current cables?
According to section 25.1707, wires and cables carrying heavy currents and associated EWIS components must be designed and installed to ensure proper physical separation and electrical isolation. This means damage to circuits associated with essential functions will be minimised under fault conditions. What do you need to consider in terms of testing?
You must consider cost and compliance as solving for the general case can require a broad test matrix to address many configurations, such as physical, electrical and environmental
Consider what is in the surrounding area (such as nearby wiring components), as this can cause separation distances greater than what has been identified for equipment. For example, the distance between a power cable and a signal cable is 2 inches, and 3 4 AWG wires with three different phases could cause arcing damage.
Engineers must also consider grounding and power separation, component separation guidance, control cable separation to prevent jamming interference, heated equipment separation, and overall compliance and safety for your organisation.
Whether you need a specific tensile strength, abrasion resistance, adhesive tapes, stainless steel cables, circuit breakers or wire identification, AFT has the resources to help you find exactly what you need for your next project.
Aircraft Cable Routing Systems: Request a Quote
From additional wires to types of wire rope, Applied Fasteners and Tooling is committed to your best interests when it comes to aerospace wire, cable, and assemblies.
Registered and AS9120 quality certified in 2014, AFT was founded to supply the aerospace and defence industries with specialised fastening products and technical support.
As a leader in the fastening system supply chain, we have military fastener supplies, countersink tooling, drilling equipment, honeycomb inserts, a quick-change track lock system, marine bonded fasteners, cable tie mounts, motorsport fasteners, and so much more.
Contact us to shop in stock, view our markets and get a quote for a personalised interaction and a value-added service throughout the product life cycle. We work in design, procurement, production, quality, maintenance and repair as a reliable partner known for our on-time delivery.