Honeycomb Inserts: Their Role in Aviation
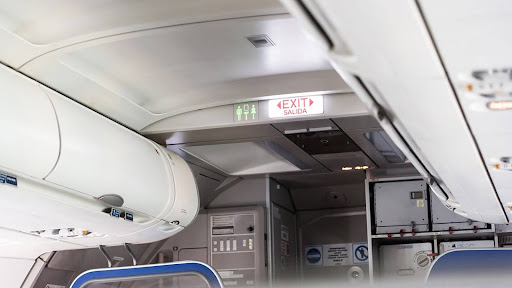
- January 11th, 2024
- Categories: Uncategorised
The honeycomb insert is a critical component of aircraft design in the aircraft industry. Constructed using aluminium sheets, these are bonded together to create a hexagonal structure resembling a beehive.
With their unique geometric design, these hexagonal cells create a high strength-to-weight ratio, forming a grid and distributing weight across the aircraft without making it heavier. Honeycomb cores are made from fibreglass, aluminium, or Nomex, a durable, fire-resistant aramid paper.
Why should you consider using honeycomb inserts for your aircraft build? With dozens of applications that ensure safety in flight, this article will explore the benefits, roles, and materials used and why you should incorporate these components into your next aerospace project.
Aircraft Repair Tools – History of Honeycomb Inserts
According to this article on Science Direct, the first artificial honeycomb insert was made with paper in China 2000 years ago, but it has evolved in design over the last century.
First used in aircraft during the early 1930s and 1940s to increase payload and reduce weight, honeycomb inserts replaced the traditional, heavier sheet, stringer, and beam support approach. It wasn’t until 1945 that the first all-aluminium sandwich panel was manufactured.
Incorporating them into sandwich panels, honeycomb inserts have become an essential structural concept in the aviation industry since the 1950s.
From 2000 onwards, all commercial and military aircraft depended on the integrity and reliability offered by honeycomb cores. In the aerospace industry, every multi-engine aeroplane uses honeycomb parts in some shape or form, such as in panelling and core fabrication.
The Role of Honeycomb Inserts in Aviation
Flight performance, durability, and safety is paramount, and the honeycomb insert assists with all these factors.
Sandwiched between two thin layers of material, the honeycomb core is used in various parts of the aircraft, such as the wings, rudder, aileron, spoiler, flap, and fuselage.
- Structural integrity. Honeycomb inserts provide a superior strength-to-weight and stiffness-to-weight ratio. This supports fuel efficiency and overall performance and is commonly used to construct the panels, fairings, and services when necessary.
- Weight reduction. Compared to solid materials, honeycomb inserts are lightweight and cost-effective.
- Rigidity and stiffness. Making components more durable, honeycomb inserts allow aircraft to withstand loads or stresses during flight. This is critical to wings and fuselage as maintaining shape supports aerodynamic performance.
- Impact absorption. A honeycomb structure can resist impact, dissipate energy across the structure and minimise damage in a collision or crash.
- Thermal insulation. Air is trapped within the honeycomb cells, adding to the insulation and sound-absorbing properties of the aircraft structure. This is important for aircraft components such as the ignition battery, auxiliary power units, and insulation against electrical fires.
- Lower Cost of Manufacturing. Manufactured using cost-effective methods, honeycomb inserts can be produced in many shapes and sizes to meet design requirements. This ease makes them an attractive option for large-scale production within the aviation industry.
Want to learn more about powerful materials that are used in aerospace applications? Read about the importance of ERG materials in advancing aerospace technology.
Types of Aircraft That Use Honeycomb Inserts
Reducing mass has always been challenging for any design engineer, and composite honeycomb structures have been a game-changer. So, what kind of aircraft can and benefit from using honeycomb inserts?
- Civil aircraft. Using enormous composites, civil aircraft benefit from high strength and stiffness, extreme temperature tolerance, and resistance to corrosion and fatigue.
- Defence aircraft. These aircraft require durable designs and were the first to be experimented on, demonstrating composites’ effectiveness. Today, there is more demand for composites in the defence industry than ever.
- Helicopters. Civil and defence helicopters are made from large amounts of aluminium honeycomb components. Parts made from honeycomb include the floor panels, side walls, and main rotor components.
- Space. In space, the materials must be strong enough to handle extreme temperature fluctuations and resist bending and shear forces. Honeycomb inserts support weight-saving measures and meet performance requirements.
Design Consideration for Composite Laminates
Integrating composite materials into aircraft requires careful consideration as a design engineer.
Fibre orientation and layering
The orientation and arrangement of original fibres within laminate can affect its mechanical properties, such as compression strength. Engineers need to design the layout for strength and stiffness strategically.
Manufacturing processes
If the process includes autoclave or resin infusion, this can affect the final properties of the composite laminate by removing pores and hardening the material. Consider the ideal performance for the material and what it will be used for.
Environmental factors
As composite laminates can be sensitive to environmental conditions, temperature variations, moisture absorption, and exposure to ultraviolet radiation must be considered during the design phase.
Joining techniques
Engineers joining composite laminates to other materials must use techniques such as fastening or adhesive bonding.
Unsure about what technique is right for you? Have a read of our comprehensive guide to welding or bonding.
Types of Inserts Used in Aviation Applications
In aviation, honeycomb inserts have hexagonal inserts made of different materials for structural strength, essential for performance and application requirements.
- Aramid fibre honeycomb inserts. Made from aramid fibres, this honeycomb insert is essential for structural components, interior panels, and fairings. It has excellent impact resistance, high strength, and is lightweight.
- Kevlar honeycomb inserts. Made from kevlar aramid fibres, this can be applied to armoured panels and pieces requiring high impact resistance, as it provides high tensile strength.
- Carbon fibre honeycomb inserts. Made of carbon fibre, this is applied to high-performing aircraft components and structural parts. It supports stiffness durability and has an excellent strength-to-weight ratio.
- Fibreglass honeycomb inserts. This insert is used for interior panels, fairings, and non-structural components.
- Stainless steel honeycomb inserts. Steel is lightweight compared to traditional wood, concrete, or hot-rolled steel, and it is applied to structural components requiring higher strength and heat resistance.
- Titanium honeycomb inserts. These are applied to areas requiring high strength and corrosion resistance.
- Hybrid honeycomb inserts. As these hexagonal cells are made from a mix of materials for specific performance, this combines the advantages of different materials for a customised aircraft application.
Applied Fasteners and Tooling – Choose Aerospace Fasteners
Are you seeking an industry leader in fastening materials and tools? At Applied Fasteners and Tooling, we have everything you need for aerospace applications, including honeycomb fasteners, Hi Lok fasteners, AN fasteners, MS fasteners, Click Bond fasteners , Materials Engineering and a range of aircraft tools for your upcoming project.
Registered and AS9120 Qualified in 2014, we supply the aerospace and defence industries with specialised products and trustworthy technical support.
Likewise, our services cover application engineering support, product development and training, product testing, program management, and repair and maintenance support.
Contact us today, and we can help you push the boundaries of what is possible.