Optimising Precision and Efficiency: Countersink Tools in Defence Manufacturing
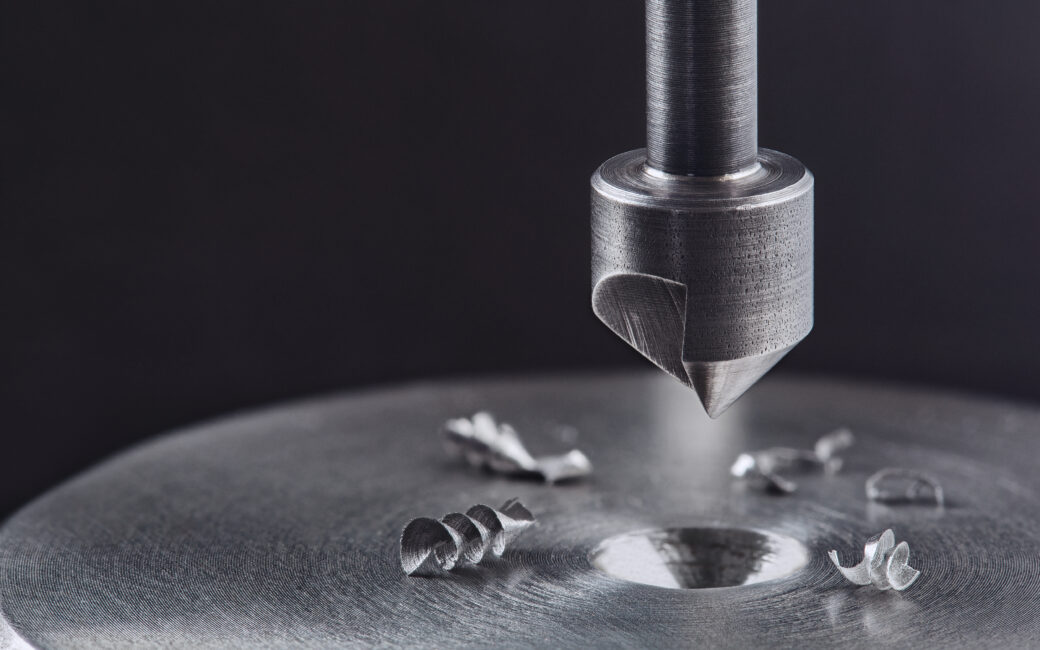
- January 15th, 2024
- Categories: Uncategorised
In the highly specialised field of defence manufacturing, tools must be reliable, accurate, and strong enough to handle all environments. One of the most important types of equipment used in this industry is countersink tools.
Countersink tools support the creation of conical holes with a drill press machine, a cone-shaped edge near the surface of this hole. This allows for fasteners such as bolts or metal screws to sit in place, successfully matching the angle and head size.
With this in mind, why are countersink tools critical to the defence industry, and how can you use them for your next project?
The Role of Countersink Tools in Defence Manufacturing
When working on engineering projects, raw materials used for countersink tooling must reflect high strength, resistance, and durability to wear and tear.
One of the key features of countersink tools is their ability to achieve a smooth finish while also preventing screws from protruding. This is why these tools are commonly used for deburring– such as using deburring tools for thin sheet metal and composite material stack-ups (a tapped or drilled hole). Countersinks can be made at any angle, often between 60 and 120 degree angle.
So, what are these tools’ specific roles, and how do they improve quality and strength for the defence industries?
1. Precision machining.
Essential for precision processes, countersink tools support accurately sized shaped recesses in components. This allows for proper fitting and alignment of fasteners.
2. Component strength.
Countersink tooling improves the strength and integrity of assembled components. Sitting flush with the surface and reducing the risk of protrusion prevents defence applications from damage.
3. Aerospace applications.
Countersink tools prepare holes in materials such as aluminium and titanium, which are critical to building aircraft and missile components.
4. Improving aerodynamics.
Creating a smooth and aerodynamic surface for military aircraft components, countersink tools reduce drag, improving performance and fuel efficiency.
5. Compatibility.
Compatible with composite materials and high-strength alloys, countersink tools can handle these materials and provide precision.
6. Easier assembly processes.
Countersink tooling allows fasteners to fit into countersunk recesses. An easier assembly makes the project building process easier and faster for an engineer.
Countersinks – Types of Materials Used
Commonly employed materials in aerospace applications include high-speed steel (HSS), aluminium, titanium, carbide, fibreglass, diamond, carbon fibre, and composite materials. The choice of these materials depends on the requirements of the application.
- High-speed steel. As a cost-effective cutter material, it is used for general application metal machining.
- Cobalt steel tools. Harder than high-speed steel, these tools are often used for cutting stainless steel or other alloys.
- Carbide grades are much harder than high-speed steel. Carbide lasts longer and wears less with several coatings.
- Industrial diamond grades. Polycrystalline diamonds (PCD) have long service lives and are used for special applications such as high-speed cutting.
Want to learn more about powerful materials that are used in aerospace applications? Read about the importance of ERG materials in advancing aerospace technology.
Countersinks – Features and Benefits
Adding to the material composition, countersinks have specific features to improve the needs of applications.
- Coated tips. This assists in the lubrication or abrasion resistance for longer tool life.
- Integral stops. Used for depth control, this prevents the countersinks from penetrating upon a specific point.
- Reverse countersinks. These don’t have a point but are useful where points could piece deeply into a given material.
- Integral pilots. Used as guides, integral pilots support countersinks in locating pre-drilled holes. This doesn’t impact the quality of the component material.
Regarding tool-material recommendations, graphite epoxy works best with carbide or a PCD countersink tool, titanium works best with carbide, aluminium works well with carbide or PCD, fibreglass pairs well with PCD, plastic works well with carbide or PCD, and mild steel should be used with HSS or carbide.
Quality Control and Surface Treatments
Quality control methods are implemented to ensure high standards in defence manufacturing. Countersink tools undergo precision testing for dimensional accuracy uniformity, undergoing surface treatments such as coatings for hardness and tool performance.
Tool Life
Why is a longer life span important for defence tools? As well as improving cost-effectiveness for manufacturing operations, this improves the overall process.
Factors Affecting Tool Life
What impacts tool life? Cutting speeds, feeds, temperature, wear resistance, and machining material. Proper tool maintenance and optimising machining will extend tool life.
Optimising Tool Life Through Geometry and Materials
The geometry, material properties and overall design of countersink tools play a role in longevity. It is critical to select the right material with superior wear resistance.
Advantages of Using Diamond Countersinks for Complex Geometries
With aircraft manufacturers, fastening two pieces of material together is critical to handle a 90-degree turn. This requires the hole to be prepared before the fastener is inserted. However, the question remains– why exactly should diamond countersinks be used for this process?
Exceptional hardness
As a tough material with wear resistance, diamond countersinks offer shape-cutting edges even when used on strong materials such as steel.
Reduced friction and heat
With excellent thermal conductivity, diamond countersinks dissipate heat better during machining. This prevents thermal damage to both the tool and the workpiece.
Versatility across materials
Diamond countersinks can be used with various metals, composites, and ceramics. In the defence industry, this is essential to complex components that rely on durability.
Reduced cutting forces
Diamond countersinks require less cutting force for defence and industrial applications, reducing the risk of tool deflection. For engineers on the job, diamond layers support machining services.
Abrasion resistance
Diamond countersinks are well-suited to abrasive wear and tear and are resistant to abrasive materials and challenging conditions.
If you want to learn more about aerospace tools and how they can help your workpiece material, learn about the versatility of grip lock ties and a comprehensive guide to flight safety.
What About Counterbore Holes?
Although similar to countersinking, counterbore holes have a cylinder shape for the top of the hole. This supports tool geometry and fasteners with flat heads.
Counterbore holes are created to seat a fastener flush. The sides are straight rather than angled, considerably more shallow than a countersink hole.
Counterbore holes provide more holding stress than a countersink hole due to the force applied by the socket head screw being parallel to the axis, and the screw or bolt is distributed evenly over a large surface.
Applied Fasteners and Tooling – Choose Aerospace Fasteners
Are you seeking an industry leader in fastening materials and tools? At Applied Fasteners and Tooling, we have everything you need for aerospace applications, including countersink tooling, countersink and counterbore cages , countersink cutters , Lubbering drilling technologies
Do you need countersink tooling to enhance hole drilling, size, and accuracy? In that case, we stock specialty tools for thin sheet material and composite material stack-ups, such as high-speed steel, carbide, and diamond tooling!
Registered and AS9120 Qualified in 2014, we supply the aerospace and defence industries with specialised products and trustworthy technical support.
Likewise, our services cover application engineering support, product development and training, product testing, program management, and repair and maintenance support.
Contact us today, and we can help you push the boundaries of what is possible.