Navigating Aircraft Repairs: Essential Tools and Techniques to Master
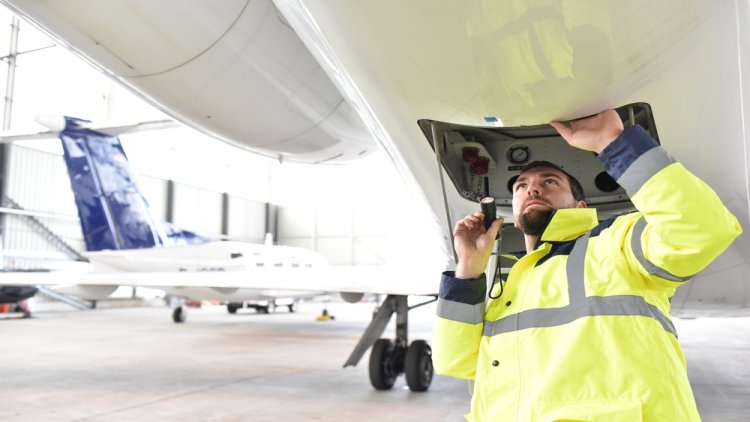
- May 24th, 2024
- Categories: Uncategorised
In recent months, the electrical faults of Boeing aircrafts have well and truly underscored the need for effective aviation repairs, maintenance, inspections, and quality control. As we have seen, electrical and engine failures can and do occur in the aviation industry, which is why it’s so important to understand the tools and techniques that allow aircrafts to remain safe and secure.
Whether you’re dealing with minor scratches or cracked to substantial sheet metal corrosion, it is important to understand the tools and options available to you as an aerospace engineer.
During today’s article, we will explore the best aircraft maintenance techniques and tips, as well as how aviation professionals use these tools to adhere to strict safety standards. After all, you may be responsible for repairing commercial planes or specialised aircraft in the defence and military fields, so here is a quick guide to different repair types.
Navigating the Aircraft Repair Process
Why is navigating aircraft repair so important in the aviation sector? From keeping strong against weather conditions and preventing major issues, there is certainly a lot to consider. Let’s explore the key aspects now.
Following manufacturer guidelines for structural repairs is critical as they provide detailed instructions for how to do them. These guidelines cover the type of repair material and specifications regarding installation methods. Guidelines also ensure that repairs are completed correctly without compromising safety or performance.
Aviation maintenance personnel must follow these guidelines as deviating from them can lead to serious safety issues or an aircraft unsafe and unfit for use.
Regular inspections help to prevent structural damage to the aircraft. These systematic processes also allow for early detection and remediation before any further deterioration happens. Structural failure can be catastrophic, so inspections help maintain compliance with regulatory requirements from aviation authorities such as the Federal Aviation Authority (FAA) or the European Union Aviation Safety Agency. Inspection intervals are mandated based on flight hours, cycles, or calendar time.
Ramp and maintenance damage. According to the International Air Transport Association, 36-40% of aircraft damage is from ramp and maintenance damage. Also known as friendly foreign object damage, this can represent significant costs to the airlines, such as causing flight delays, cancellations, connecting flights, or flight rotations.
Ageing aircraft. In-flight structural failure can occur–as shown by the Aloha Airlines Boeing 7370-200–such as the upper fuselage being ripped open and separated from the aircraft, resulting in multiple-site damage and corrosion. This has called for selecting new aircraft alloys with better chemical control or changes in heat treatment tempers.
Examples of design improvements to reduce corrosion on the Boeing 777 include enhanced drainage in the keel of the aircraft, the sealing of faying surfaces in corrosion-prone areas, the application of improved finish systems, liberal use of corrosion-preventive compounds, implementing a good corrosion control maintenance program, and improved access for inspection.
Aircraft Repair – Common Repair Techniques
Repair techniques used for aircraft structures depend on the type and extent of the damage. The most common techniques include replacing damaged parts with new ones, repairing these parts with composite materials, or patching damages with metallic patches. So, what are some repair techniques?
Composite material repair
Licensed to Australian-owned private company Helitech Industries Pty Ltd in 1990, Helitech Industries partnered with DSTG in 1995 and developed a composite bonded repair for the US Air Force C-141 Starlifter.
This technique can restore a weakened structure since it provides strength without adding excess weight compared to some metals. Composite material repair is used in commercial airlines and military aircraft belonging to the Royal Australian Air Force and the US and Belgian Air Forces. It has even been adapted to repair gun carriages using an electroformed nickel material.
This type of repair is structurally efficient, prevents stress-corrosion cracking, has advantages over bolting or riveting, offers uniform load transfer, seals interfaces to stop leakage and creates minimal damage to the parent structure. Composite material repair is applied across the Australian Defence Force (ADF) fleet and can be applied to civilian aircraft.
Sheet metal patching repair
Rivet fasteners are used to repair localised damages in the aircraft and secure them. Minor damage could include missing or damaged rivets, scratches, a small dent on a sheet metal surface, a small crack, or a corroded sheet metal surface.
Missing or damaged rivets
- Rivets missing on an airframe are common and could result from corrosion or underlying damage. Always find the root cause. If a rivet is damaged, it will look slightly slanted or raised. Place a small feeler gauge (.020) under the head of the rivet, as it could be stretched.
- If a rivet is loose or missing, you must replace it with the exact type originally used, and you can determine this from the manufacturer or service manual. AD rivets are the most common, and this will have a dimple on the head of the rivet.
- A damaged rivet needs to be removed and replaced, and you do not want to enlarge the rivet hole. Determine the correct drill bit size; when properly installed, rivet holes are drilled slightly larger than the rivet diameter. You will usually encounter a 3/32 or a 1/8-inch diameter rivet, which will expand to fill the hole.
- Drilling the hole involves a hand drill- a pneumatic drill is preferred- and inserting the proper-sized drill bit that is sharp and slightly smaller than the rivet. Don’t attempt to drill into the sheet metal itself. After drilling into the head, use a pin punch to pry off the rivet head, then one slightly smaller than the rivet shank to drive it out from the hole. The objective is to remove the rivet without damaging the sheet metal or enlarging the hole.
Corroded sheet metal
- Corroded sheet metal weakens a structure, so all signs of corrosion must be removed. To remove corrosion, use fine sandpaper, Scotch Brite pads, or aluminium wool. Never use steel wool or a steel brush!
- Once corrosion is removed, the aluminium needs to be acid-etched. Washing the product with Poly Fiber E-2310 Adid Etch diluted with water removes oil and light corrosion, providing a firm primer bond. The part is then thoroughly rinsed, and the surface is washed with E-2300 Conversion Coating, supporting primer adhesion. Allow to completely dry. The damaged area can then be primed and repainted.
Scratch or small dent
- Scratches must be repaired to stop corrosion from forming. Polish out a scratch or gauge using a high-speed grinder with an attached Cratex abrasive wheel. Rubberised and designed to use on sheet metal, removing the damaged area is easier.
- A small dent can be fixed using a filler material. Poly-Fiber’s SuperFil is an ideal filler as it doesn’t shrink over time. Apply using a squeegee and allow it to dry overnight; you can then sand it smooth and touch up the paint.
Small cracks
- Common on sheet metal aeroplanes, cracking can develop in an engine cowling. Using a small drill bit, you can “stop-drill” the crack by drilling at each end of the crack to prevent further development. Vibration can cause the crack to extend if proper repairs are not made, so rivet a small patch over the area using the same metal found on the original piece.
- If you have a piece of .032 skin that has a crack, stop-drill both ends and cut a small piece of .032 aluminium to patch it. A rounded or several-sided patch is preferable over a square patch. After marking the proper rivet layout, you can drill out the holes and fasten the patch with clecos. Once satisfied, remove clecos and apply zinc chromate to the back of the patch.
Installing a new rivet
- If you can reach the back of the rivet, this can be a simple task. After placing the rivet in the hole, determine whether you can drive it or squeeze it. Reach inside the structure with a buckling bar or apply a rivet squeezer, but if this isn’t possible, you will need to use a blind rivet.
- Eliminating the need to cut an access hole to buck a standard rivet, a blind rivet is very useful. However, the access hole must be cut if you can’t reach the backside. Blind rivets on the market include friction-lock Cherry Rivets, CherryMax Rivets, mechanical-lock cherry rivets, and more.
Adhesive bonding techniques
In use for over 50 years, these tools are a direct competitor to riveting. Adhesive bonding is used to bond stringers to skins for fuselage, as well as wing construction to stiffen the structures against buckling or metallic honeycomb cores inside metal skins for flight control component structures, such as elevators, ailerons, or spoilers.
- Bonding agents play a role in repairing damaged sections, adhering them together after removing unwanted debris or corrosion. Adhesives are non-metallic structures capable of joining materials through surface bonding-adhesion-with the bond possessing adequate internal strength, which is cohesion.
- Adhesive material used for these purposes falls into three groups: metal/metal hot cure, metal/metal honeycomb hot cure, and metal-to-metal cold cure.
- The most important category of structural adhesives is that of the metal-to-metal hot cure types and a comparison of their room-temperature mechanical properties. Subsonic aircraft are designed to perform within a temperature range of +80 -55 degrees Celsius, and designers must consider the properties of the adhesives at this temperature.
- Adhesive systems are used on aircraft. British Aerospace aircraft, predecessor aircraft manufacturers, and Fokker aircraft have used Redux 775 in liquid, powder, and film form for making primary aircraft structures.
Most hot bonding operations are carried out in large autoclaves, although some hydraulic steam-heated pressers are still used. To learn more about adhesive bonding for aircraft systems, check out what is better for navy environments, bonding or welding.
Composite patching
As a lesser-known technique, this involves composite material to reinforce damaged areas on the aircraft’s structure instead of traditional metal patching. Composite patching can be lightweight, easier to apply in hard-to-reach areas, has design flexibility, is more fatigue-resistant, has higher damage tolerance, and is less prone to corroding.
Different composite bonded repair joints are increasingly used to repair metallic and non-metallic structures. External patch repair is faster and widely used for aircraft to keep them in serviceable condition.
A drying procedure is often required before applying the repair patch to remove all moisture. The damaged location is then cleaned, repair laminates are placed, and the repair patch/scarf is cured on top of the original parent structure-aircraft part using a heating blanket under vacuum.
Ultrasonic testing
Using high-frequency sound waves, ultrasonic testing detects defects or changes in the material properties within an object, almost like a microscope. This can detect hidden cracks or flaws within an aircraft’s structure.
With this in mind, there are often challenges faced during inspections or structural repairs. Challenges could be assessing areas of the aircraft’s structure due to design complexity, special scaffolding or platforms to gain access, or dealing with hidden damage from corrosion or fatigue. Specialised equipment is used to detect and diagnose these issues.
For another in-depth look at aircraft, have a look at aircraft cable management and safety in flight.
Applied Fasteners and Tooling – Aerospace Tools
Whether you need NAS Fasteners, AN Fasteners, Hi-Lok Fasteners, Cherry Fasteners, Rivet Removal Tools, Drill Bits for different types of aircraft or appropriate Hand Tools that meet aviation regulations for flight safety, Applied Fasteners and Tooling have everything you need for the maintenance of aircraft.
Supplying the best technological advancements to several markets, we understand the critical aspects of efficient operations and safe navigation. Meeting the Quality Assurance Procurement Requirements, we supply and support quality assembly tooling consumables for aerospace, space, defence platforms, and industrial programs worldwide.
Registered and AS9120 quality certified in 2014, contact us today for personalised interaction, technical support, maintenance, repair, and on-time delivery.